Методы компенсации упругих деформаций в высоконагруженных рейках
Введение в проблематику упругих деформаций
Высоконагруженные зубчатые рейки играют критическую роль во множестве промышленных приложений, от станкостроения до тяжелого машиностроения, автоматизированных систем и производственных линий. В условиях передачи значительных усилий и высоких нагрузок неизбежно возникают упругие деформации, которые могут существенно влиять на точность позиционирования, равномерность движения, износостойкость и долговечность зубчато-реечных передач.
Упругие деформации в зубчато-реечных передачах обусловлены комплексом физических явлений, происходящих под действием нагрузки. При передаче крутящего момента возникают контактные напряжения в зоне сопряжения зубьев рейки и шестерни, изгибные напряжения у основания зубьев, а также напряжения кручения и изгиба в телах элементов передачи. Эти напряжения вызывают деформации, которые, даже оставаясь в пределах упругости материала, могут достигать значений, критичных для функциональных характеристик механизма.
Важно: По данным исследований, упругие деформации могут приводить к погрешностям позиционирования до 50-70 мкм в незащищенных системах, что для прецизионного оборудования является недопустимым.
Первостепенной задачей при проектировании высоконагруженных реечных передач является не столько исключение деформаций (что физически невозможно), сколько их компенсация или контроль — применение методов, позволяющих минимизировать негативное влияние деформаций на рабочие характеристики системы. Данная статья представляет собой комплексный обзор современных подходов к компенсации упругих деформаций, их теоретическое обоснование, методики расчета и практические аспекты внедрения.
Типы деформаций в зубчатых рейках
Для понимания механизмов компенсации необходимо классифицировать типы упругих деформаций, возникающих в высоконагруженных зубчатых рейках:
Локальные деформации
Относятся к изменениям геометрии отдельных элементов рейки:
- Контактные деформации — возникают в зоне контакта зубьев рейки и шестерни под действием контактных напряжений. Характеризуются формированием площадки контакта вместо теоретической линии.
- Изгибные деформации зубьев — происходят под действием тангенциальной составляющей усилия в зацеплении. Приводят к отклонению рабочего профиля зуба от теоретического.
- Деформации сдвига зубьев — вызываются касательными напряжениями и проявляются как смещение вершины зуба относительно его основания.
Глобальные деформации
Затрагивают рейку как целостную конструкцию:
- Деформации тела рейки — изгиб, кручение и растяжение-сжатие основания рейки под действием распределённой нагрузки.
- Деформации монтажного основания — упругие прогибы и перекосы кронштейнов, направляющих и посадочных мест, на которых закреплена рейка.
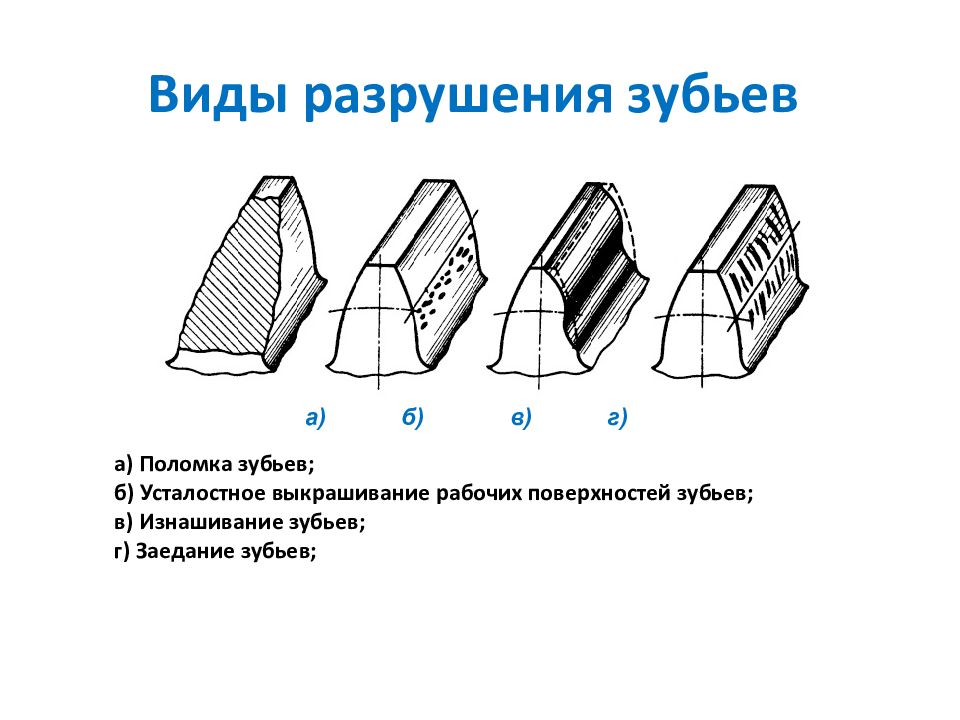
Рис. 1. Схематическое представление основных типов деформаций в зубчатых рейках под нагрузкой.
Тип деформации | Причины возникновения | Характерный диапазон | Влияние на работу передачи |
---|---|---|---|
Контактные деформации | Герцевские напряжения в зоне контакта | 5-25 мкм | Повышенный износ, нагрев, шум |
Изгиб зубьев | Тангенциальная составляющая нагрузки | 10-40 мкм | Погрешности перемещения, вибрации |
Деформации тела рейки | Распределённые нагрузки, неравномерность креплений | 20-100 мкм | Нарушение плавности хода, ускоренный износ |
Температурные деформации | Неравномерный нагрев при работе | 15-60 мкм | Изменение зазоров, заклинивание |
Важно отметить, что вышеперечисленные типы деформаций редко проявляются изолированно. Как правило, наблюдается комплексное воздействие различных деформаций, что усложняет задачу их компенсации и требует системного подхода.
Методы измерения и диагностики деформаций
Перед внедрением любого метода компенсации упругих деформаций необходимо точно определить их характер, величину и распределение. Современная инженерная практика располагает следующими инструментами для измерения и диагностики деформаций:
Экспериментальные методы
- Тензометрия — применение тензодатчиков, закрепляемых на критических участках рейки, позволяет измерить деформации в реальном времени под нагрузкой.
- Лазерная интерферометрия — высокоточный метод, основанный на анализе интерференционной картины, позволяющий выявить деформации с точностью до долей микрометра.
- Цифровая корреляция изображений (DIC) — оптический метод, использующий сравнение цифровых изображений поверхности до и после нагружения для визуализации полей деформаций.
- Акустическая эмиссия — регистрация упругих волн, возникающих при деформации материала, позволяет определить моменты возникновения критических нагрузок.
Расчетные методы
- Метод конечных элементов (МКЭ) — численное моделирование, позволяющее предсказать характер деформаций на этапе проектирования.
- Аналитические расчеты — основаны на классических формулах сопротивления материалов и теории упругости.
Пример расчета контактных деформаций в зубчатом зацеплении:
Величина сближения контактирующих поверхностей в зоне зацепления зубьев рейки и шестерни может быть рассчитана по формуле Герца:
где:
- δ — величина контактной деформации, мм
- F — нагрузка на единицу длины контактной линии, Н/мм
- μ₁, μ₂ — коэффициенты Пуассона материалов рейки и шестерни
- E₁, E₂ — модули упругости материалов рейки и шестерни, МПа
- ρ₁, ρ₂ — радиусы кривизны контактирующих поверхностей, мм
Численный пример: При нагрузке F = 500 Н/мм, для стальной рейки и шестерни (E = 2.1×10⁵ МПа, μ = 0.3) с приведенным радиусом кривизны ρ = 8 мм, получаем контактную деформацию δ ≈ 0.017 мм или 17 мкм.
Комплексное применение экспериментальных и расчетных методов позволяет создать детальную картину деформационного поведения зубчатой рейки и разработать оптимальную стратегию компенсации.
Основные методы компенсации деформаций
Методы компенсации упругих деформаций в высоконагруженных зубчатых рейках можно разделить на несколько основных категорий:
- Конструктивные методы — изменение геометрии и конструкции реечной передачи для снижения или перераспределения деформаций;
- Технологические методы — специальные приемы изготовления и обработки, направленные на минимизацию последствий деформаций;
- Эксплуатационные методы — приемы установки, регулировки и обслуживания, обеспечивающие компенсацию деформаций;
- Активные методы — системы с обратной связью, динамически корректирующие положение элементов передачи.
Далее рассмотрим наиболее эффективные методы из каждой категории более подробно.
Предварительное нагружение и преднатяг
Метод предварительного нагружения основан на создании начальных деформаций, противоположных тем, которые возникают при эксплуатационных нагрузках. Это позволяет заранее компенсировать ожидаемые упругие деформации.
Механические системы преднатяга
В современной практике применяются следующие системы создания преднатяга:
- Двухшестерневые механизмы с разделенным потоком мощности — схема с двумя шестернями, работающими на одну рейку с предварительным угловым смещением, создающим начальное напряжение.
- Системы с упругими элементами — применение пружин, эластомерных вставок или других упругих элементов для создания предварительного контакта с определенным усилием.
- Гидравлические и пневматические системы преднатяга — использование давления жидкости или газа для создания и регулирования силы прижатия шестерни к рейке.
Расчет параметров двухшестерневой системы преднатяга:
Величина предварительного момента M₀, необходимого для компенсации упругих деформаций, может быть определена по формуле:
где:
- M₀ — предварительный момент преднатяга, Н·м
- M_max — максимальный рабочий момент при эксплуатации, Н·м
- k — коэффициент преднатяга, обычно принимается в диапазоне 0.1-0.3
Угол предварительного смещения между шестернями α определяется выражением:
где C_φ — крутильная жесткость системы привода, Н·м/рад.
Пример: Для системы с максимальным моментом M_max = 2500 Н·м, коэффициентом преднатяга k = 0.2 и крутильной жесткостью C_φ = 15000 Н·м/рад, получаем M₀ = 500 Н·м и α = 0.067 рад ≈ 3.8°.
Эффективность метода преднатяга зависит от точности определения эксплуатационных нагрузок и характера деформаций. При правильном расчете и реализации преднатяг позволяет уменьшить мертвый ход и повысить жесткость системы на 40-60%.
Геометрическая коррекция профиля зубьев
Метод геометрической коррекции заключается в намеренном изменении теоретически правильной геометрии зубьев рейки таким образом, чтобы под нагрузкой деформированный профиль максимально приближался к идеальному.
Основные типы геометрических модификаций:
- Модификация профиля по высоте — создание бочкообразности или конусности зуба для компенсации изгибных деформаций.
- Модификация профиля по длине — изменение толщины зуба вдоль длины рейки для компенсации деформаций тела рейки.
- Коррекция угла зацепления — небольшое отклонение угла эвольвентного профиля от стандартного значения.
- Высотная коррекция (корригирование) — смещение инструмента при нарезании зубьев для изменения толщины зуба у основания и вершины.
Расчет параметров модификации профиля зуба:
Величина модификации профиля зуба Δs, необходимая для компенсации изгибных деформаций, может быть вычислена по формуле:
где:
- Δs — величина модификации (отклонение от теоретического профиля), мкм
- δ_f — максимальная изгибная деформация зуба под расчетной нагрузкой, мкм
- h — текущая высота точки профиля от основания зуба, мм
- h_f — полная высота зуба, мм
Пример: При максимальной изгибной деформации δ_f = 35 мкм и в точке профиля на высоте h = 0.6·h_f, необходимая величина модификации составит Δs = 35 · (1 - (0.6)²) = 35 · 0.64 = 22.4 мкм.
Геометрическая коррекция требует высокоточного изготовления и является пассивным методом, эффективным для систем с предсказуемым и постоянным характером нагрузки. Современные технологии обработки позволяют реализовать модификации профиля с точностью до 1-2 мкм.
Материаловедческие решения
Выбор материалов с оптимальными упругими характеристиками и применение специальных покрытий играют важную роль в компенсации деформаций высоконагруженных реек.
Современные материалы для зубчатых реек:
- Высоколегированные инструментальные стали (X153CrMoV12, HS 6-5-2-5) — обеспечивают высокий модуль упругости и износостойкость.
- Азотированные стали (34CrAlNi7, 31CrMoV9) — формируют твердый поверхностный слой при сохранении вязкой сердцевины.
- Композитные материалы с углеродным волокном — позволяют создавать конструкции с заданными характеристиками жесткости в разных направлениях.
- Металлокерамические композиции — сочетают высокую твердость керамики с вязкостью металлической матрицы.
При выборе подходящего материала рекомендуется ознакомиться с доступными вариантами зубчатых реек от проверенных производителей, которые обеспечивают необходимые сертификаты качества и технические характеристики.
Специальные покрытия:
- DLC (Diamond-Like Carbon) — алмазоподобные углеродные покрытия, снижающие трение и износ.
- Многослойные PVD-покрытия (TiN, TiCN, TiAlN) — повышают твердость поверхности и сопротивление контактным нагрузкам.
- Покрытия на основе нитрида кремния — обеспечивают высокую износостойкость в условиях граничного трения.
Материал | Модуль упругости, ГПа | Предел текучести, МПа | Твердость, HRC | Относительное сопротивление деформациям |
---|---|---|---|---|
Сталь 42CrMo4 (закаленная) | 210 | 900-1100 | 48-52 | 1.0 (базовый уровень) |
Сталь X153CrMoV12 | 215 | 1400-1600 | 58-62 | 1.5 |
Азотированная сталь 31CrMoV9 | 210 | 1100-1300 | 58-64 (поверхность) | 1.4 |
Металлокерамика на основе карбида вольфрама | 550-650 | 2200-2400 | 70-72 (эквивалент) | 2.8 |
Инженерный факт: Применение специальных DLC-покрытий с коэффициентом трения 0.05-0.1 позволяет снизить контактные деформации на 15-20% за счет уменьшения тангенциальных составляющих нагрузки.
Оптимальный выбор материала и покрытия должен осуществляться на основе комплексного анализа условий эксплуатации, характера нагрузок и требований к долговечности системы.
Расчёт параметров компенсации деформаций
Эффективность методов компенсации упругих деформаций зависит от точности определения необходимых параметров коррекции. Рассмотрим основные расчетные методики, применяемые в инженерной практике.
Расчет изгибных деформаций зубьев рейки
Максимальная изгибная деформация зуба рейки под нагрузкой может быть вычислена по формуле:
где:
- δ_f — изгибная деформация зуба, мм
- F_t — тангенциальная составляющая силы в зацеплении, Н
- h — высота зуба, мм
- E — модуль упругости материала рейки, МПа
- I — момент инерции сечения зуба, мм⁴
Расчет деформаций тела рейки
Прогиб рейки как балки на опорах под действием сосредоточенной силы в середине пролета:
где:
- δ_r — прогиб рейки, мм
- F — нагрузка, Н
- L — расстояние между опорами (точками крепления), мм
- E — модуль упругости, МПа
- J — момент инерции поперечного сечения рейки, мм⁴
Расчет параметров системы с преднатягом
Оптимальная сила преднатяга F₀ для двухшестерневой системы может быть определена из условия:
где F_max — максимальная рабочая нагрузка.
Суммарная жесткость системы с преднатягом:
где C₁ и C₂ — жесткости элементов системы, C_пр — дополнительная жесткость от преднатяга.
Комплексный пример расчета параметров компенсации:
Рассмотрим зубчатую рейку модуля m = 4 мм, с высотой зуба h = 9 мм, изготовленную из стали (E = 2.1×10⁵ МПа), установленную с шагом крепления L = 250 мм и работающую под нагрузкой F_t = 6000 Н.
Шаг 1: Определяем момент инерции сечения зуба:
I = b·h³/12 = 25·9³/12 = 1518.75 мм⁴
Шаг 2: Рассчитываем изгибную деформацию зуба:
δ_f = F_t·h³/(3·E·I) = 6000·9³/(3·2.1×10⁵·1518.75) = 0.0379 мм = 37.9 мкм
Шаг 3: Вычисляем момент инерции сечения рейки:
J = b·H³/12 = 25·40³/12 = 133333 мм⁴
Шаг 4: Определяем прогиб рейки между опорами:
δ_r = F·L³/(48·E·J) = 6000·250³/(48·2.1×10⁵·133333) = 0.0139 мм = 13.9 мкм
Шаг 5: Рассчитываем необходимую силу преднатяга:
F₀ = 0.25·F_max = 0.25·6000 = 1500 Н
Шаг 6: Определяем параметры геометрической коррекции:
Модификация профиля вершины зуба: Δs = 0.7·δ_f = 0.7·37.9 = 26.5 мкм
Данные расчеты позволяют определить необходимые параметры для эффективной компенсации упругих деформаций в рассматриваемой реечной передаче.
Практические примеры и кейсы
Рассмотрим несколько практических примеров внедрения методов компенсации упругих деформаций в различных отраслях промышленности.
Кейс 1: Тяжелый портальный станок с длинной реечной передачей
Проблема: Неравномерность перемещения портала из-за деформаций реек под нагрузкой, приводящая к погрешностям обработки до 0.15 мм на длине 12 м.
Примененное решение:
- Реализована система двухшестерневого привода с преднатягом 28% от номинальной нагрузки
- Применена геометрическая коррекция профиля зубьев с учетом расчетных деформаций
- Использована сегментная конструкция рейки с регулируемыми стыками
- Внедрена система мониторинга нагрузок с адаптивной корректировкой усилия преднатяга
Результат: Снижение погрешности позиционирования до 0.03 мм, увеличение срока службы реек на 40%, существенное снижение вибраций.
Кейс 2: Прецизионный координатно-расточной станок
Проблема: Высокие требования к точности (±2 мкм) при значительных усилиях резания.
Примененное решение:
- Рейки выполнены из специального сплава с высоким модулем упругости (270 ГПа)
- Применена технология DLC-покрытия рабочих поверхностей
- Реализована система гидростатической разгрузки направляющих
- Внедрена система активной компенсации с датчиками перемещения и корректирующими приводами
Результат: Обеспечена стабильная точность позиционирования в пределах ±1.5 мкм при нагрузках до 70% от расчетных максимальных.
Кейс 3: Роботизированная система перемещения тяжелых грузов
Проблема: Значительная неравномерность хода при перемещении грузов разной массы (от 500 кг до a5 тонн).
Примененное решение:
- Внедрена адаптивная система управления с датчиками нагрузки
- Применена комбинация реечной передачи с системой гидравлической компенсации
- Реализована ступенчатая система преднатяга, регулируемая в зависимости от массы груза
Результат: Обеспечение плавности перемещения с отклонением скорости не более 2% во всем диапазоне нагрузок, увеличение производительности системы на 25%.
Сравнительный анализ методов компенсации
Выбор оптимального метода компенсации упругих деформаций зависит от конкретных условий применения и требований к системе. Ниже представлен сравнительный анализ основных методов по ключевым параметрам.
Метод компенсации | Эффективность снижения деформаций | Сложность реализации | Стоимость внедрения | Надежность | Применимость при переменных нагрузках |
---|---|---|---|---|---|
Предварительное нагружение (преднатяг) | 70-85% | Средняя | Средняя | Высокая | Средняя |
Геометрическая коррекция профиля | 60-75% | Высокая | Средняя | Очень высокая | Низкая |
Применение материалов с высоким модулем упругости | 40-60% | Низкая | Высокая | Высокая | Высокая |
Оптимизация конструкции рейки | 50-70% | Средняя | Средняя | Высокая | Средняя |
Активные системы компенсации с обратной связью | 85-95% | Очень высокая | Очень высокая | Средняя | Очень высокая |
Гидравлические системы компенсации | 75-85% | Высокая | Высокая | Средняя | Высокая |
Комбинированные методы | 80-95% | Высокая | Высокая | Высокая | Высокая |
Важное примечание: В современной инженерной практике наиболее эффективным является комплексный подход, сочетающий несколько взаимодополняющих методов компенсации упругих деформаций.
Для систем с высокими требованиями к точности и работающих в широком диапазоне нагрузок рекомендуется сочетание методов преднатяга и геометрической коррекции с элементами активной компенсации.
Рекомендации по внедрению
Успешная реализация методов компенсации упругих деформаций требует системного подхода и соблюдения определенной последовательности действий:
Этапы внедрения методов компенсации:
- Детальный анализ эксплуатационных условий:
- Определение диапазона рабочих нагрузок
- Анализ режимов работы (постоянный, переменный, циклический)
- Выявление критичных параметров точности
- Расчет и моделирование деформаций:
- Применение аналитических методов расчета
- Компьютерное моделирование методом конечных элементов
- Прототипирование и экспериментальная верификация
- Выбор оптимальной стратегии компенсации:
- Определение целевых показателей эффективности
- Технико-экономическое обоснование выбранных методов
- Разработка технической документации
- Реализация выбранных методов:
- Изготовление компонентов с требуемыми характеристиками
- Монтаж и регулировка механизмов компенсации
- Настройка систем управления и контроля
- Тестирование и верификация:
- Измерение фактических деформаций
- Оценка точности позиционирования
- Анализ динамических характеристик
- Оптимизация и доводка:
- Корректировка параметров преднатяга
- Тонкая настройка геометрии
- Калибровка системы активной компенсации
Практические рекомендации:
- Для тяжелонагруженных систем: Комбинировать преднатяг с геометрической коррекцией, уделять особое внимание жесткости креплений рейки.
- Для прецизионных систем: Применять активные методы компенсации с обратной связью, использовать материалы с минимальным гистерезисом упругих деформаций.
- Для систем с переменными нагрузками: Отдавать предпочтение адаптивным системам преднатяга с регулируемым усилием.
- Для длинных реек: Использовать сегментную конструкцию с возможностью индивидуальной регулировки каждого сегмента.
- При выборе реек: Обращаться к проверенным поставщикам, предлагающим зубчатые рейки с документированными техническими характеристиками и возможностью консультации по особенностям монтажа.
Внимание! При реализации систем с преднатягом необходимо учитывать возможное увеличение трения и износа. Рекомендуется применение современных смазочных материалов и покрытий с низким коэффициентом трения.
Рекомендации по выбору зубчатых реек
При выборе зубчатых реек для высоконагруженных применений критически важно учитывать не только стандартные технические параметры (модуль, число зубьев, материал), но и возможность эффективной компенсации упругих деформаций в конкретных условиях эксплуатации. В каталоге зубчатых реек представлен широкий ассортимент изделий, отличающихся конструктивными особенностями и эксплуатационными характеристиками.
Для оптимального выбора рекомендуется обратить внимание на следующие аспекты:
- Соответствие класса точности — для прецизионных систем выбирайте рейки с повышенным классом точности (5-6 по DIN), обеспечивающие минимальные отклонения профиля
- Возможность регулировки — для длинных реек предпочтительны конструкции с регулируемыми креплениями, позволяющими компенсировать деформации при монтаже
- Термообработка поверхности — рейки с индукционной закалкой зубьев или общей термообработкой обеспечивают повышенную стабильность геометрических параметров под нагрузкой
- Состояние поверхности — шлифованные рейки обеспечивают более плавное зацепление и меньшие динамические нагрузки, что снижает деформации
Инженеры компании "Иннер Инжиниринг" готовы помочь в выборе оптимальной зубчатой рейки с учетом специфики вашего проекта и предоставить консультацию по методам компенсации упругих деформаций для конкретного применения.
Заключение
Компенсация упругих деформаций в высоконагруженных зубчатых рейках представляет собой комплексную инженерную задачу, решение которой требует глубокого понимания физических процессов, происходящих в механической системе, и применения современных методов расчета, моделирования и конструирования.
Как показывает практика, наибольшую эффективность демонстрирует комплексный подход, сочетающий несколько взаимодополняющих методов компенсации. При этом выбор конкретных методов должен основываться на детальном анализе эксплуатационных условий и требований к системе.
Развитие новых материалов, технологий обработки и систем управления открывает дополнительные возможности для совершенствования методов компенсации упругих деформаций. Особенно перспективными направлениями являются интеллектуальные системы с прогнозирующими алгоритмами, аддитивные технологии для создания оптимизированных структур и новые композитные материалы с запрограммированными деформационными характеристиками.
Корректно реализованные методы компенсации упругих деформаций позволяют существенно повысить точность, долговечность и надежность зубчато-реечных передач, что, в свою очередь, обеспечивает повышение качества и эффективности работы технологического оборудования в целом.
Источники информации
- Кудрявцев В.Н., Кирдяшев Ю.Н., Гинзбург Е.Г. "Зубчатые передачи". — М.: Машиностроение, 2021.
- Балакшин Б.С. "Теория и практика технологии машиностроения". — СПб.: Политехника, 2019.
- ISO 6336-1:2019 "Calculation of load capacity of spur and helical gears".
- Niemann G., Winter H. "Maschinenelemente: Band 2: Getriebe allgemein, Zahnradgetriebe". — Springer-Verlag, 2023.
- Kumamoto H., Suzuki K., Terauchi Y. "Effect of tooth profile modification on the load distribution of helical gears". — Bulletin of JSME, 2022, Vol. 65, No. 633.
- Анурьев В.И. "Справочник конструктора-машиностроителя". — М.: Машиностроение, 2020.
- Решетов Д.Н. "Детали машин". — М.: Машиностроение, 2018.
- Ковалев М.П., Народецкий М.З. "Расчет высокоточных шарикоподшипников". — М.: Машиностроение, 2019.
Ограничение ответственности: Данная статья имеет исключительно ознакомительный характер и предназначена для инженерно-технических специалистов. Представленные расчеты и методики требуют адаптации для конкретных условий применения. Авторы и издатель не несут ответственности за возможные последствия использования информации без дополнительной профессиональной проверки и консультации.
Купить зубчатые рейки по выгодной цене
Компания Иннер Инжиниринг предлагает широкий выбор зубчатых реек. Выберите необходимые компоненты для вашего проекта и приобретите их у нас с гарантией качества и надежной доставкой.
Заказать сейчас