Корпуса подшипников SNL
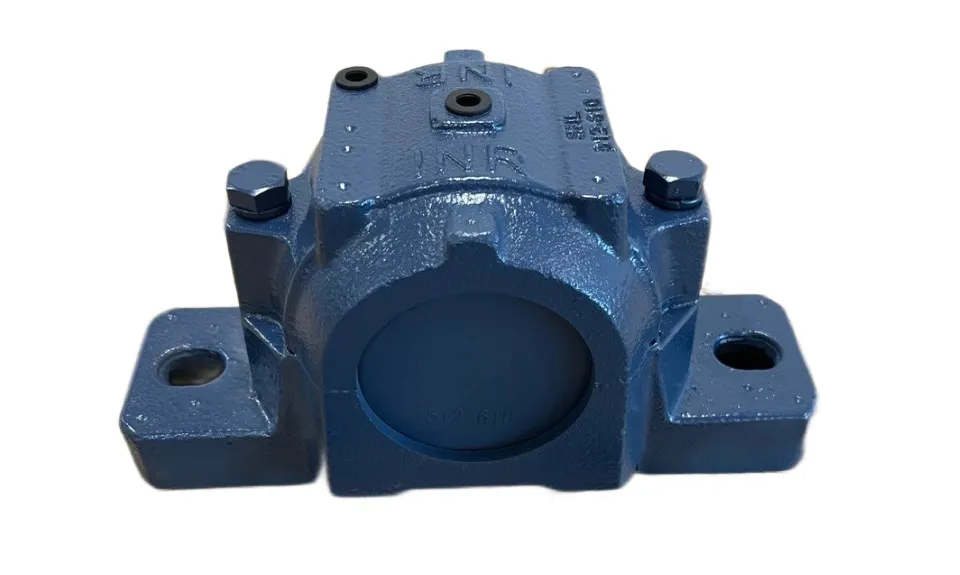
Технические Условия - Корпуса Подшипников Качения "INNER"
Настоящие технические условия распространяются на корпуса подшипников качения (далее – корпусов) бренда "INNER", изготавливаемые из серого чугуна маркой не ниже СЧ-20 по ГОСТ 1412-85.
Чертеж разъёмных корпусов, а также прайс на продукцию, предоставляются по запросу.
1. Общие Требования
-
Химический состав и механические свойства корпусов соответствуют ГОСТ 1412. Допускается отклонение от химического состава с сохранением механических свойств.
-
Посадочный диаметр под подшипник выполняется по полю допуска H8. Значение параметра шероховатости Rz посадочных поверхностей под подшипник и опорных торцов заплечников не более 20 мкм. После механической обработки допускаются на плоскостях межоперационные переходы от инструмента, высотой не более 0,1 мм. Значение параметра шероховатости Rz, на дне канавок после обработки, допускается до 40 мкм.
-
Точность отливки 10-0-0-10 по ГОСТ Р 53464.
2. Требования к Дефектам
На корпусах не допускаются:
- Дефекты на маркировке.
- Дефекты в механически обработанных отверстиях и резьбе.
- Дефекты, превышающие 50% от толщины стенки на которой они расположены.
- Дефекты, влияющие на эстетический вид верхней части крышки корпуса.
3. Последовательность Производства Разъёмных Корпусов
- Изготовление форм для отливок заготовок разъемных корпусов
- Заливка форм чугуном СЧ 20
- Извлечение заготовок из формы
- Пескоструйная обработка литых заготовок
- Грунтовка предварительно обработанных заготовок
- Фрезеровка дна основания корпусов, мест стыковки крышки и основания корпуса
- Сверление отверстий в крышке и основании, нарезание резьбы для болтов крепления крышки и корпуса
- Расточка места установки подшипника
- Финальная внешняя механическая обработка корпуса в сборе
- Повторная грунтовка обработанных изделий
- Покраска изделий
4. Описание Процессов Изготовления
-
Вначале изготовляется литейная модель из пластика, полученная методами быстрого прототипирования, копирующая будущую деталь. Модель, закреплённая на подмодельной плите, засыпается формовочной смесью, заполняющей пространство между ней и двумя открытыми ящиками (опоками). Отверстия и полости в детали образуются с помощью размещённых в форме литейных песчаных стержней, копирующих форму будущего отверстия. Насыпанная в опоки смесь уплотняется прессованием. Места контакта формовочной смеси с металлом покрываются огнеупорным напылением.
-
Образовавшиеся полости заливаются расплавом чугуна через специальные отверстия — литники.
-
После остывания форму разбивают и извлекают отливку. После чего отделяют литниковую систему.
-
Что бы удалить неровности, полученные в процессе литья, заготовки проходят пескоструйную обработку.
-
Перед передачей в цех механической обработки заготовки корпусов покрывают специальной грунтовкой.
-
В цехе механической обработки отлитые заготовки проходят финальную обработку. Все установочные места самого корпуса фрезеруются, так же фрезеруются места стыковки крышки и основания корпуса.
-
Рассверловка отверстий под масленку, установочные штифты, намечаются места для дополнительных отверстий. Резьба для болтов крепления нарезается в предварительно засверленных отверстиях.
-
После стыковки крышки и основания корпуса происходит обработка посадочного места под подшипник.
-
Финальная внешняя обработка корпуса в сборе позволяет убрать некоторые неровности, полученные в литейном цехе.
-
После механической обработки детали повторно грунтуются.
-
После покраски изделия высыхают естественным способом и отправляются на упаковку.
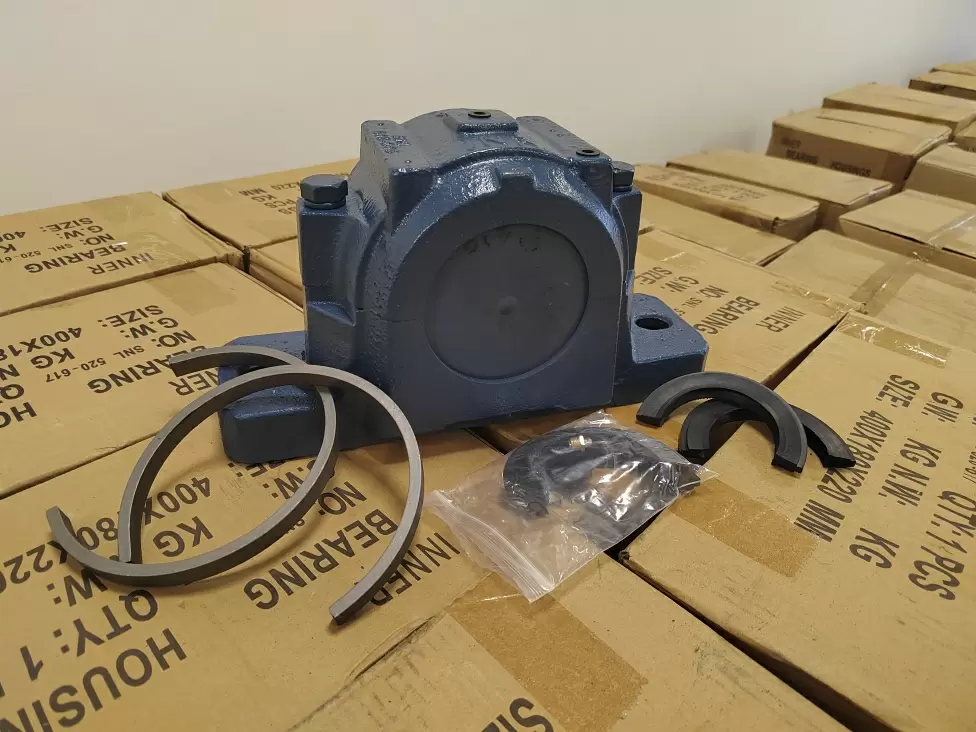
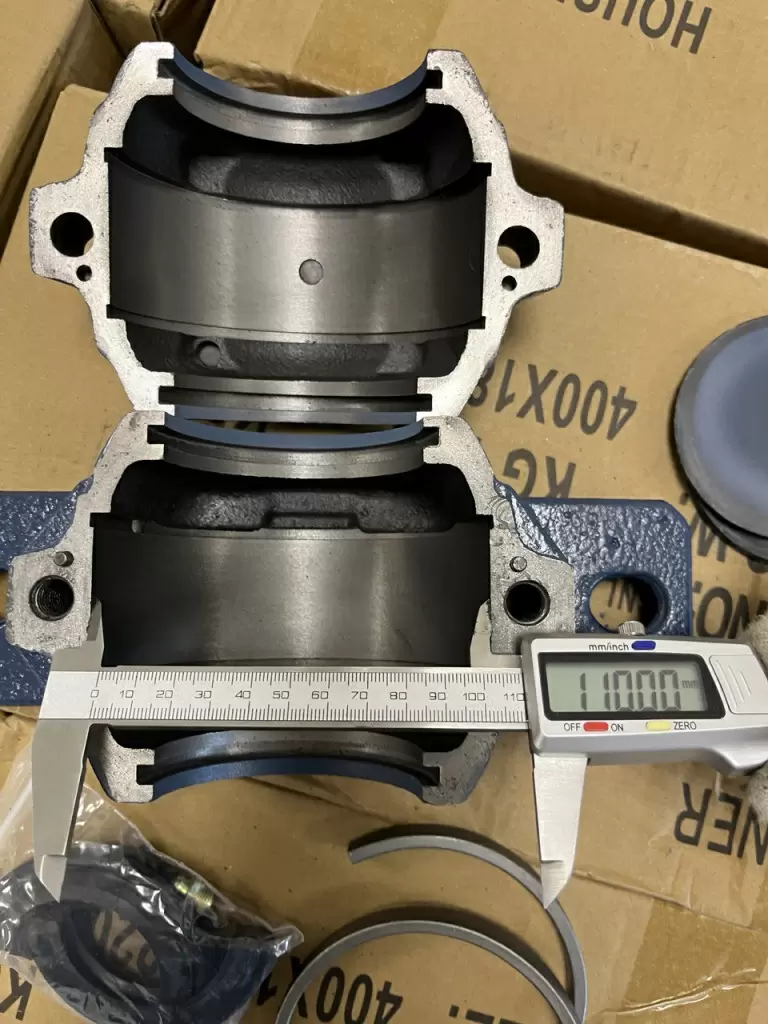
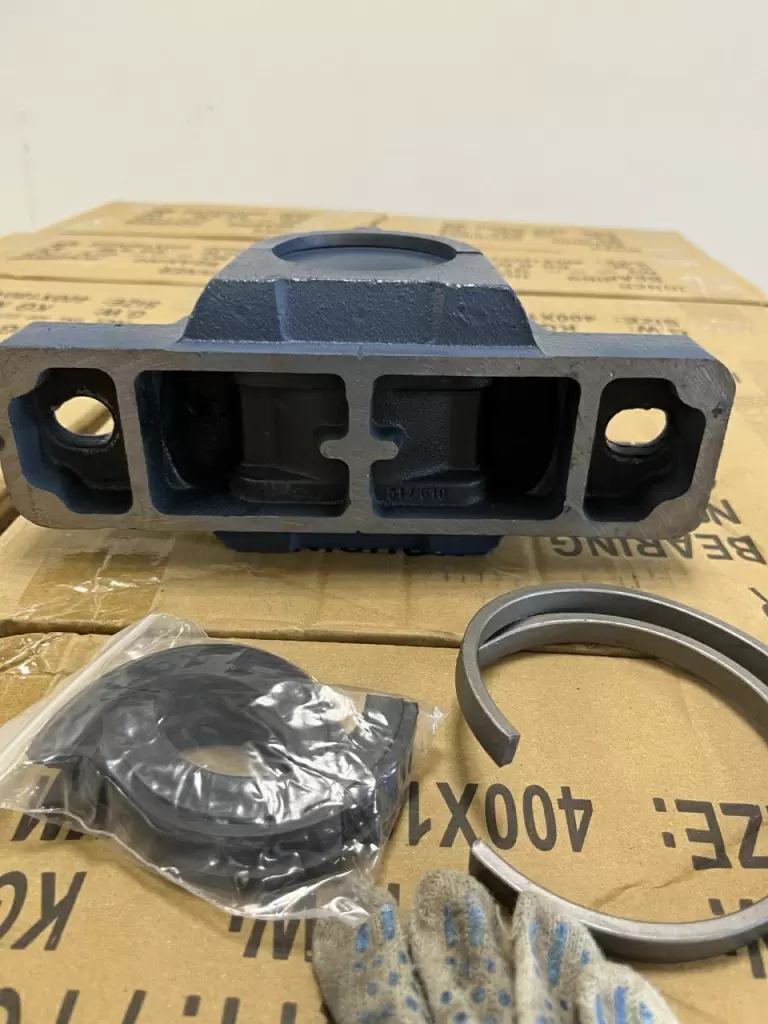