Шпонка на валу
Шпоночные соединения: теория, расчет, применение
Шпоночные соединения являются одним из распространенных типов разъемных соединений, предназначенных для передачи крутящего момента между валом и насаженной на него деталью, например, зубчатым колесом, шкивом или муфтой. Надежность и долговечность этих соединений напрямую зависят от правильности выбора и установки шпонки, а также от точности изготовления сопрягаемых деталей.
Что такое шпонка?
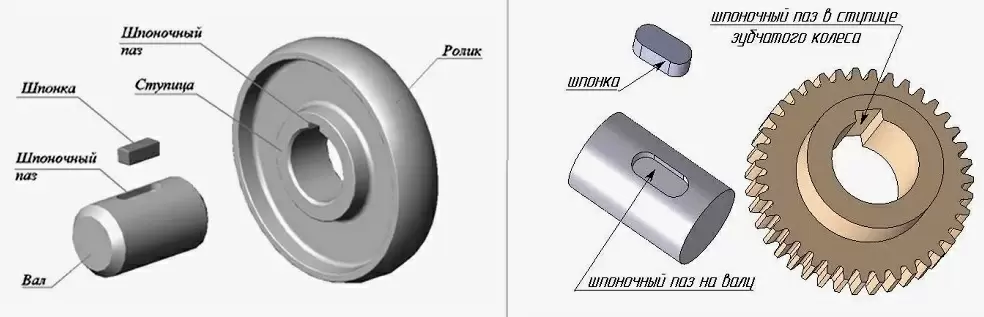
Шпонка – это небольшая деталь, обычно прямоугольной или клиновидной формы, которая вставляется в шпоночный паз на валу и в соответствующий паз на насаживаемой детали. Она предотвращает проскальзывание и вращение деталей относительно друг друга, обеспечивая жесткое соединение для передачи крутящего момента.
Основные типы шпонок
- Призматические шпонки: Наиболее распространенный тип, имеющий прямоугольное сечение.
- Клиновые шпонки: Имеют трапециевидное сечение и обеспечивают более надежное крепление, особенно при переменных нагрузках.
- Сегментные шпонки: Используются для соединений с небольшими углами поворота.
- Тангенциальные шпонки: Применяются в соединениях, подвергающихся значительным динамическим нагрузкам.
В данной статье основное внимание будет уделено призматическим шпонкам, как наиболее распространенному типу.
Шпоночное соединение на вал
Для передачи крутящего момента шпонка должна плотно прилегать к пазам вала и насаживаемой детали. В соответствии с ГОСТ, существуют стандартные размеры шпонок и пазов под них, которые зависят от диаметра вала. Выбор шпоночного соединения определяется рядом факторов, таких как:
- Диаметр вала.
- Передаваемый крутящий момент.
- Тип нагрузки.
- Скорость вращения.
Размеры шпонок и пазов на валах
Размеры шпонок и пазов регламентируются стандартами ГОСТ 23360-78 и ГОСТ 23361-78. Приведем примеры размеров для некоторых валов, согласно стандарту:
Диаметр вала (мм) | Ширина шпонки (b), мм | Высота шпонки (h), мм | Длина шпонки (l), мм* |
---|---|---|---|
10 | 4 | 4 | до 20 |
18 | 6 | 6 | до 36 |
25 | 8 | 7 | до 50 |
32 | 10 | 8 | до 63 |
40 | 12 | 8 | до 80 |
50 | 14 | 9 | до 100 |
* Длина шпонки может быть выбрана исходя из длины ступицы, в пределах указанных в таблице значений.
Примечание: Размеры, приведенные в таблице, являются номинальными. Для обеспечения правильной посадки, они должны учитывать допуски и посадки согласно ГОСТ 23360-78.
Посадка шпонки на вал
Посадка шпонки на вал – это зазор или натяг между шпонкой и пазами вала и насаживаемой детали. Выбор посадки зависит от типа нагрузки и требуемой точности соединения.
- Посадка с зазором: Шпонка свободно входит в пазы, обеспечивая простоту сборки.
- Посадка с натягом: Шпонка вставляется с усилием, обеспечивая более надежное соединение и исключая люфт.
Посадки шпонок определяются по ГОСТ 25346-89 и выбираются в зависимости от условий эксплуатации и требуемой точности соединения. В большинстве случаев используют посадки типа H7/h6 или P7/n6 (где H7 - посадка паза в насаживаемой детали, h6 или n6 - посадка шпонки в пазах вала).
Пример: Для вала диаметром 25 мм выбирается призматическая шпонка 8x7 мм, а для посадки типа H7/h6 допуски составляют:+0.019/+0.000 мм на паз на валу и 0.000/-0.010 на шпонку.
Длина шпонки на валу
Длина шпонки обычно выбирается в зависимости от длины ступицы насаживаемой детали. Она должна быть достаточной для передачи требуемого крутящего момента, но не должна быть настолько длинной, чтобы выходить за пределы ступицы. Стандартная длина шпонки указана в таблице выше.
Установка шпонки на вал
Установка шпонки требует аккуратности и соблюдения технологического процесса. Обычно она включает следующие шаги:
- Очистка пазов от грязи и заусенцев.
- Установка шпонки в паз вала.
- Насадка детали на вал, обеспечивая совмещение паза.
- Проверка плотности посадки.
Для посадки с натягом может потребоваться использование пресса или нагрева ступицы детали.
Допуск на шпонку на валу
Допуски на шпонки и пазы вала регламентируются ГОСТ. Они обеспечивают правильную посадку и предотвращают перекосы и заклинивание. Размеры с допусками обеспечивают сопряжение шпонки и пазов с нужными зазорами или натягами, необходимыми для работы в различных условиях.
2 шпонки на валу
В некоторых случаях для передачи больших крутящих моментов, или для обеспечения точной фиксации положения детали, используют два шпоночных паза на валу. При этом шпонки располагают либо симметрично друг относительно друга (на 180 градусов), либо под другим углом. Использование двух шпонок позволяет увеличить площадь контакта и тем самым обеспечить более надежную передачу момента.
Паз под шпонку на валу
Паз под шпонку на валу выполняется с высокой точностью и чистотой поверхности. Для пазов предусмотрены допуски на ширину и глубину, а также шероховатость поверхности. При изготовлении пазов применяют фрезерование, протягивание или электроэрозионную обработку.
Срезало шпонку на валу
Срезание шпонки – это ситуация, когда шпонка разрушается под воздействием избыточного крутящего момента. Это может произойти из-за перегрузки, неправильного выбора шпонки, дефектов материала или неправильной установки. Если шпонка срезается, необходимо тщательно проанализировать причины и заменить шпонку, выбрав более подходящий размер или материал, при необходимости.
Крепление шпонки на валу
Шпонка может быть закреплена на валу путем плотной посадки в паз, а также с использованием дополнительных средств, таких как винты или штифты. Однако основное удержание шпонки обеспечивается за счет сил трения между шпонкой и пазами, а так же плотной посадки на шпоночные пазы.
Посадка на вал со шпонкой
При выборе посадки на вал со шпонкой необходимо учитывать не только допуски шпоночных соединений, но и допуски на диаметры вала и насаживаемой детали. Это важно для обеспечения соосности и правильного распределения нагрузки.
Для чего нужна шпонка на валу?
Шпонка обеспечивает жесткую фиксацию вращающихся деталей относительно друг друга, что позволяет эффективно передавать крутящий момент. Это предотвращает проскальзывание и вращение деталей на валу, обеспечивая надежную работу механизма. Она используется в различных отраслях промышленности: машиностроении, станкостроении, автомобилестроении и т.д.
Шпонка на вал редуктора
Шпоночные соединения активно применяются в редукторах для передачи крутящего момента между валами и зубчатыми колесами. Надежность и правильный выбор шпонки играют важную роль в долговечной работе редуктора.
Примеры расчетов и выбора шпонки
Пример 1: Выбор шпонки для вала 25 мм
Для вала диаметром 25 мм по ГОСТ 23360-78 выбираем призматическую шпонку 8х7 мм. Длина шпонки выбирается в зависимости от длины ступицы.
Пример 2: Расчет усилия при срезе
Пусть на вал 25 мм передается момент силы 100 Нм. Вычислим силу, действующую на шпонку:
F = M / r, где:
- M - момент силы (100 Нм)
- r - радиус вала (0.0125 м)
Таким образом, F = 100 / 0.0125 = 8000 Н. Это сила, которая может привести к срезу шпонки. Прочность шпонки на срез должна быть выше расчетной, для обеспечения надежности соединения.
Заключение
Шпоночные соединения - это важные элементы в механизмах и машинах, обеспечивающие передачу крутящего момента. Правильный выбор шпонки, точное изготовление пазов, соблюдение допусков и технологического процесса установки – залог надежной и долговечной работы оборудования. Данная статья предоставляет общую информацию о шпоночных соединениях, однако для точных расчетов и выбора шпонок необходимо обращаться к специализированной технической литературе и стандартам.
Дополнительные аспекты шпоночных соединений: выбор, расчет, проблемы
В предыдущей статье мы рассмотрели основные понятия, связанные со шпоночными соединениями. Эта статья расширяет тему, углубляясь в вопросы выбора, расчета и типичных проблем, возникающих при эксплуатации шпоночных соединений. Мы также рассмотрим различные материалы шпонок и способы их фиксации для предотвращения ослабления.
Материалы для шпонок
Материал шпонки играет ключевую роль в надежности соединения. Выбор материала зависит от условий эксплуатации, передаваемого крутящего момента и требуемой прочности. Основными материалами для изготовления шпонок являются:
- Сталь: Наиболее распространенный материал для шпонок, обладающий хорошей прочностью и износостойкостью. Используются различные марки стали, включая Ст3, Ст45, 40Х, 45Х и другие.
- Инструментальная сталь: Используется для шпонок, работающих в условиях высоких нагрузок и высоких температур.
- Латунь и бронза: Применяются в случаях, когда необходима коррозионная стойкость и снижение трения.
- Полимеры: Применяются для работы в условиях невысоких нагрузок, где необходима легкость и устойчивость к коррозии.
Выбор материала шпонки также зависит от требований ГОСТ на конкретное соединение. Важно учитывать как прочностные свойства материала, так и его устойчивость к воздействию окружающей среды.
Расчет шпоночного соединения на прочность
Основным расчетом для шпоночного соединения является проверка на прочность. Шпонка может разрушиться из-за:
- Среза: Шпонка срезается при перегрузке.
- Смятия: Шпонка деформируется в результате воздействия сил.
Расчет на срез производится по формуле:
τ = F / (b * l) ≤ [τ]
где:- τ - напряжение среза
- F - усилие, действующее на шпонку
- b - ширина шпонки
- l - длина шпонки
- [τ] - допускаемое напряжение среза (зависит от материала шпонки)
Расчет на смятие производится по формуле:
σ = 2 * F / (h * l) ≤ [σ]
где:- σ - напряжение смятия
- F - усилие, действующее на шпонку
- h - высота шпонки
- l - длина шпонки
- [σ] - допускаемое напряжение смятия (зависит от материала шпонки)
Пример расчета:
Пример расчета на прочность
Имеем вал диаметром 40 мм, передаваемый момент 200 Нм, шпонка стальная 12х8 мм, длина 60 мм, допускаемое напряжение среза [τ] = 70 МПа и смятия [σ] = 140 МПа.
1. Определим усилие на шпонке: F = M / r = 200 / (0.020) = 10000 Н
2. Рассчитаем напряжение среза: τ = F / (b * l) = 10000 / (0.012 * 0.060) = 13.89 МПа
3. Рассчитаем напряжение смятия: σ = 2 * F / (h * l) = 2 * 10000 / (0.008 * 0.060) = 41.67 МПа
В данном примере, расчетные напряжения среза и смятия меньше допускаемых, что говорит о прочности шпонки в данном соединении.
Фиксация шпонки на валу
В некоторых случаях требуется дополнительная фиксация шпонки, чтобы предотвратить ее выпадение или смещение. Это особенно важно при переменных нагрузках и высоких скоростях вращения. Методы фиксации:
- Винтами: Шпонка может быть зафиксирована винтами, вкручиваемыми в вал через отверстия в шпонке.
- Штифтами: Используются штифты, которые вводятся в отверстия, выполненные в шпонке и валу.
- Пружинными элементами: Пружинные шайбы и другие элементы могут удерживать шпонку в пазу.
- Стопорными кольцами: Используются для осевой фиксации деталей на валу, которые могут удерживать шпонку.
Выбор метода фиксации зависит от требований к соединению и условий эксплуатации. Дополнительные элементы фиксации, обеспечивают более надежную работу соединения и повышают его безопасность.
Проблемы, связанные со шпоночными соединениями
Несмотря на простоту, шпоночные соединения могут сталкиваться с рядом проблем, которые могут повлиять на работоспособность соединения:
- Разрушение шпонки: Возникает из-за перегрузки, неправильного выбора шпонки, усталости материала.
- Износ пазов: В результате трения между шпонкой и пазами вала и ступицы.
- Ослабление посадки: Из-за вибрации и циклических нагрузок.
- Коррозия: При работе в агрессивной среде.
Решение проблем, связанных с шпоночными соединениями, включает регулярный осмотр, контроль за соблюдением условий эксплуатации, использование качественных материалов и правильный монтаж.
Влияние качества изготовления шпоночных соединений
Качество изготовления шпоночных соединений играет важную роль в их надежности и долговечности. Основные аспекты, влияющие на качество:
- Точность размеров пазов и шпонки: Несоблюдение допусков может привести к неверной посадке и неравномерному распределению нагрузки.
- Качество поверхности пазов: Шероховатость поверхности пазов должна быть в пределах норм для обеспечения правильного контакта.
- Прямолинейность шпонки: Искривление шпонки может привести к ее неравномерной работе и поломке.
- Качество материала шпонки: Неправильный выбор материала может снизить прочность и износостойкость шпонки.
Контроль качества шпоночных соединений на каждом этапе производства является необходимым условием их надежной работы.
Примеры использования шпоночных соединений в различных отраслях
Пример 1: Редукторы
Шпоночные соединения используются в редукторах для передачи крутящего момента от вала двигателя к валу редуктора и между валами шестерен. В редукторах шпонки подвергаются высоким и переменным нагрузкам, что требует точного расчета и выбора надежных материалов.
Пример 2: Насосы
В насосах шпоночные соединения применяются для передачи момента от двигателя к рабочему колесу насоса. Они должны обеспечивать надежную фиксацию деталей, особенно при работе с жидкостями под давлением. При этом требуется учитывать не только нагрузку, но и устойчивость к коррозии.
Пример 3: Станки
В станках шпоночные соединения используются для соединения валов, зубчатых колес, шкивов и других вращающихся элементов. В станках требуется высокая точность и надежность соединения, что обуславливает высокие требования к качеству изготовления шпонок и пазов.
Заключение
Шпоночные соединения остаются важным и широко применяемым методом передачи крутящего момента в машиностроении. Их надежность зависит от многих факторов, включая выбор материала, точность изготовления, правильный расчет и условия эксплуатации. Эта статья расширяет понимание шпоночных соединений и предоставляет дополнительные аспекты, которые необходимо учитывать при проектировании и обслуживании механизмов.