Соединение деталей
Соединения деталей: Виды, Способы, Примеры и Расчеты
Введение
Соединения деталей - это неотъемлемая часть любого механического устройства. Они обеспечивают сборку отдельных элементов в единую конструкцию, передачу механических усилий и правильное функционирование механизма. В этой статье мы рассмотрим основные виды соединений, способы их реализации, приведем примеры и рассмотрим базовые расчеты.
Классификация соединений
Соединения деталей классифицируются по нескольким признакам:
- По возможности разборки:
- Разъемные: Соединения, которые могут быть разобраны без разрушения соединяемых деталей.
- Неразъемные: Соединения, разборка которых ведет к разрушению либо самих деталей, либо соединительных элементов.
- По способу соединения:
- Механические: Используют механические элементы (болты, винты, штифты и т.д.).
- Сварные: Соединение путем сварки.
- Клееные: Соединение с использованием клеев.
- Пайка: Соединение с использованием припоя.
- По типу взаимодействия:
- Геометрические: Основанные на форме сопрягаемых поверхностей (клиновые, шлицевые, шпоночные).
- Фрикционные: Использующие силы трения для передачи нагрузки (резьбовые, зажимные).
Разъемные соединения
Разъемные соединения позволяют многократно собирать и разбирать узлы без их повреждения. Основные виды:
Резьбовые соединения
Резьбовые соединения являются наиболее распространенными. Они используют болты, винты, гайки и шпильки.
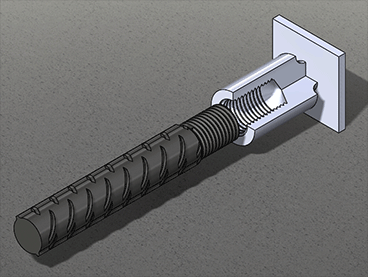
Пример расчета: Рассчитаем усилие затяжки болтового соединения.
Предположим, нужно соединить две стальные пластины с помощью болта M10 (диаметр резьбы 10 мм). Материал болта – сталь 8.8. Для данного материала предел текучести σт = 640 МПа. Запас прочности примем n = 1.5. Допустимое напряжение σдоп = σт/n = 640 МПа / 1.5 = 426.7 МПа.
Площадь резьбы болта Aрезьбы = π (d/2)2 ≈ π (8.4/2)2 ≈ 55.4 мм2. Сила затяжки Fзатяжки = Aрезьбы * σдоп ≈ 55.4 мм2 * 426.7 Н/мм2 ≈ 23642 Н ≈ 23.6 кН
Шпоночные соединения
Шпоночные соединения служат для передачи крутящего момента между валом и вращающейся деталью.
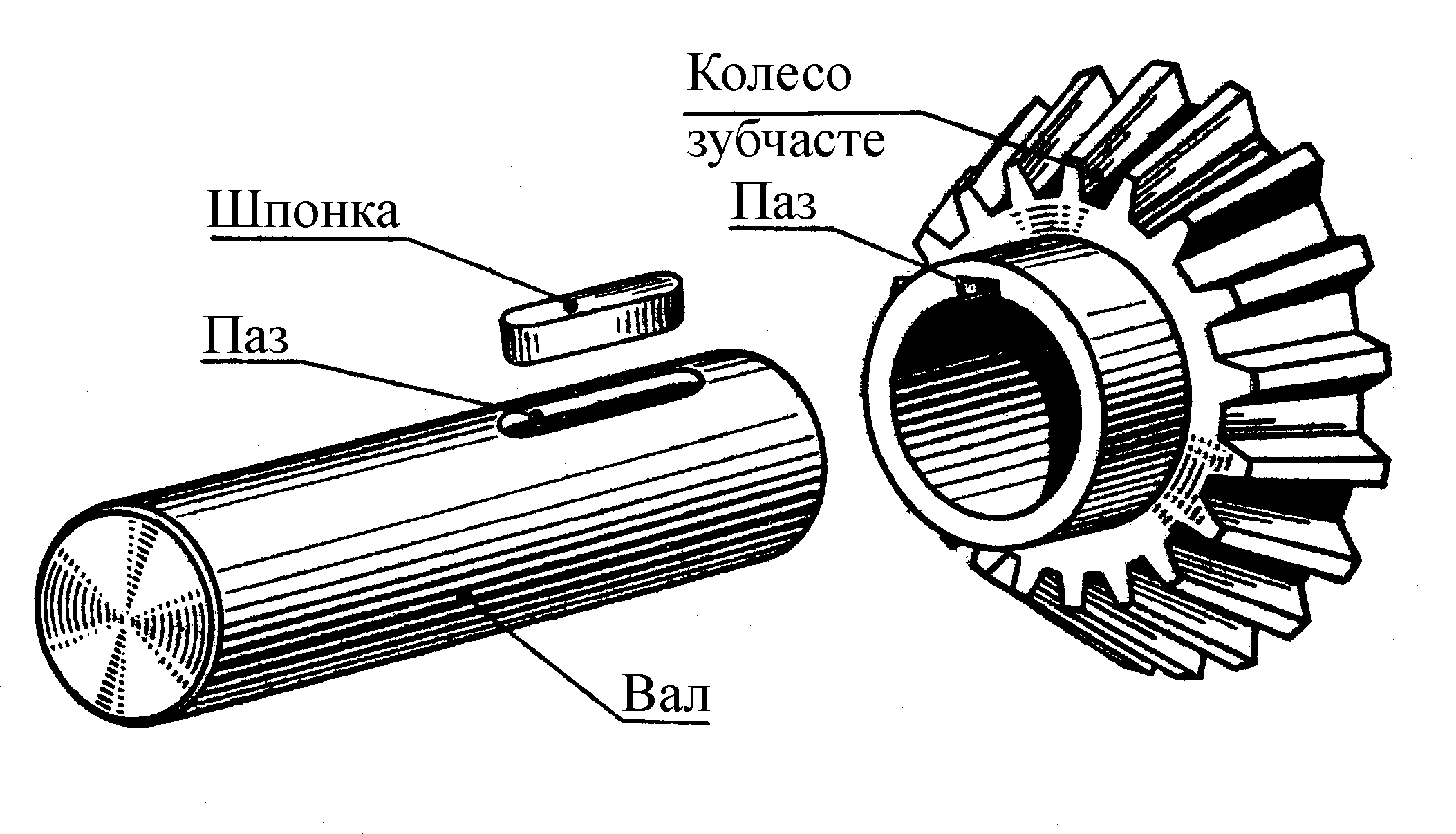
Пример: Передача крутящего момента шпоночным соединением.
Предположим, нужнопередать момент 200 Н·м через вал диаметром 30 мм. Используется шпонка шириной 8 мм и высотой 7 мм. Длина шпонки 50 мм. Материал шпонки – сталь с допустимым напряжением на смятие σсм = 120 МПа.
Сила, действующая на шпонку F = M/r = 200 Нм / (0.03м/2) = 13333 Н
Площадь смятия шпонки Асм = (h/2) * l= (7мм/2) * 50 мм = 175 мм2.
Напряжение смятия σсм= F/ Асм = 13333 Н/ 175 мм2 = 76.2 МПа < 120 МПа, следовательно, условие прочности по смятию соблюдается.
Шлицевые соединения
Шлицевые соединения используются для передачи больших крутящих моментов и точной фиксации деталей.


Пример: Расчёт числа шлицев.
Для передачи момента M=150 Н·м на валу d=30 мм, при σсм = 100 МПа. Примем высоту шлицов h = 5 мм. Найдем площадь смятия Aсм = (h * d * π) / 2. Примем количество шлицев z=8. Получим Aсм = (0.005 * 0.03 * π * 8 )/2=0.00188 м2. Далее найдем усилие F = M/r = 150/(0.03/2)=10000 Н. Напряжение σсм = F/ Aсм = 10000 Н / 0.00188 м2=5319148 Па = 53.2 МПа < 100 МПа, следовательно, условие прочности соблюдается.
Клиновые соединения
Клиновые соединения используются для точной фиксации и передачи нагрузки.
Неразъемные соединения
Неразъемные соединения обеспечивают прочное и долговечное соединение, которое не предназначено для разборки.
Сварные соединения
Сварка используется для соединения металлических деталей путем их нагрева и плавления.
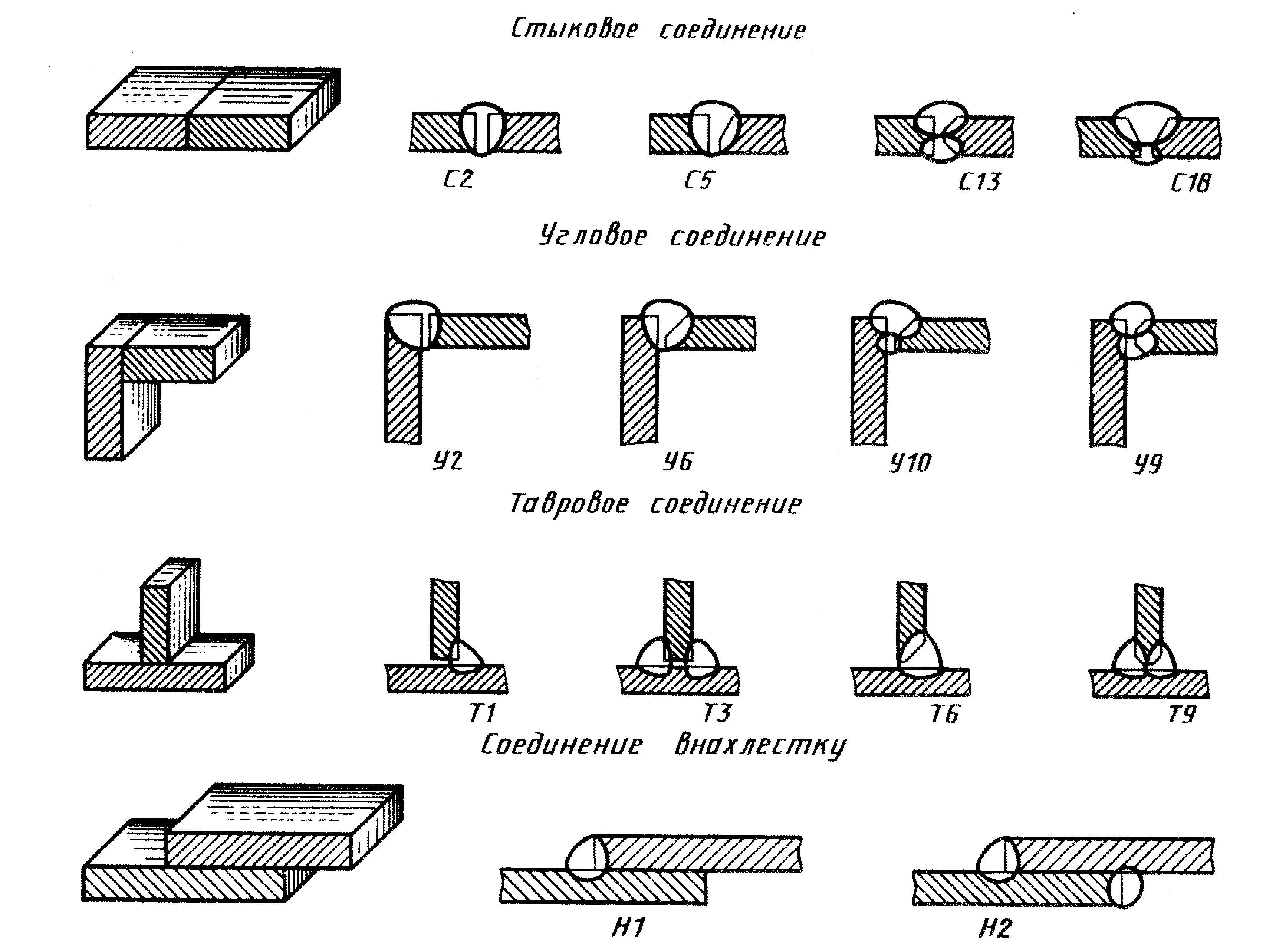
Пример: Расчет толщины сварного шва
Соединим две пластины толщиной 10 мм. Материал сталь с пределом прочности σв=400 МПа. Рассчитаем шов при усилии F = 10000 Н. Допустимое напряжение на разрыв примем σдоп = σв/n = 400 МПа/2 =200 МПа. Площадь сечения шва Ашва= F / σдоп = 10000 Н / 200 МПа=50 мм2. Длина шва l=100 мм, тогда толщина шва t = Ашва / l = 50 мм2 /100 мм = 0.5 мм. В реальности минимальная толщина шва должна быть не менее толщины самого материала, т.е. 10 мм в нашем случае.
Клееные соединения
Клееные соединения используются для соединения разнородных материалов.
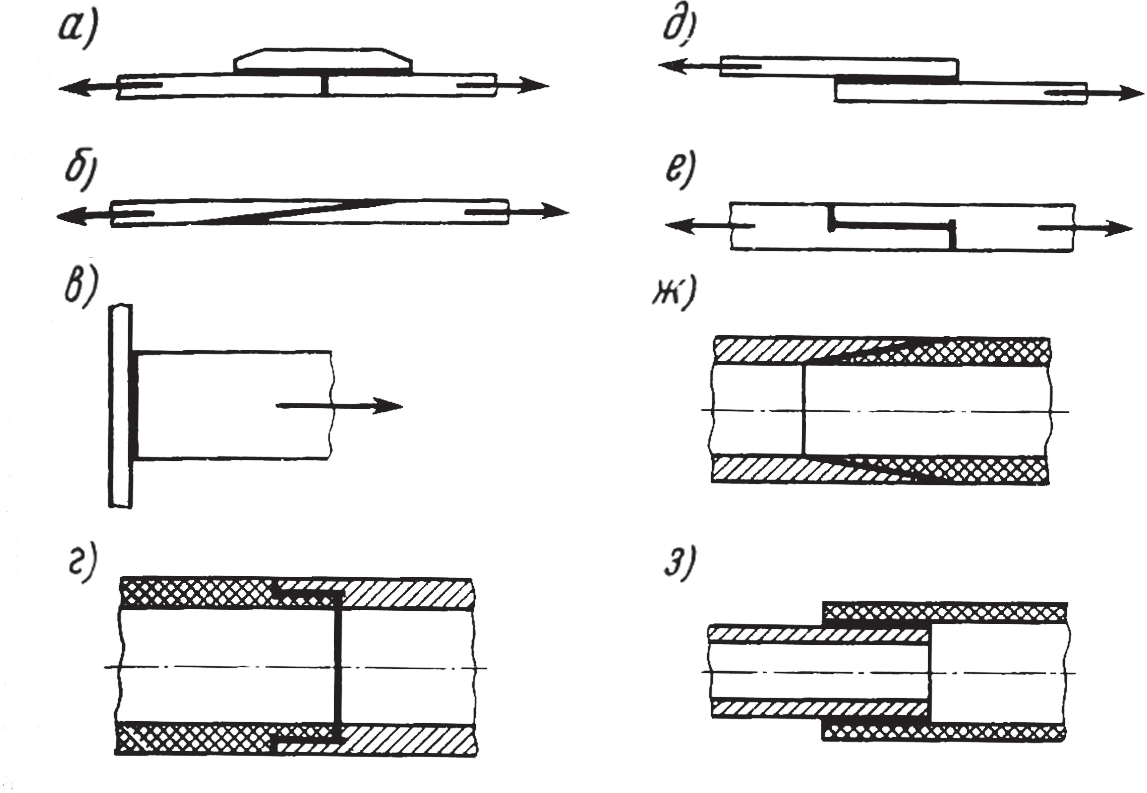
Разновидности клеевых соединений деталей: а – соединения встык с накладкой; б – с косым стыком; в – стыковое; г – стыковое соединение труб одинакового диаметра; д – внахлестку; е – внахлестку шпунтовое; ж – с косым стыком соединение труб одного диаметра; з – внахлестку (телескопическое) соединение труб разного диаметра
Пайка
Пайка используется для соединения металлических деталей с использованием припоя.
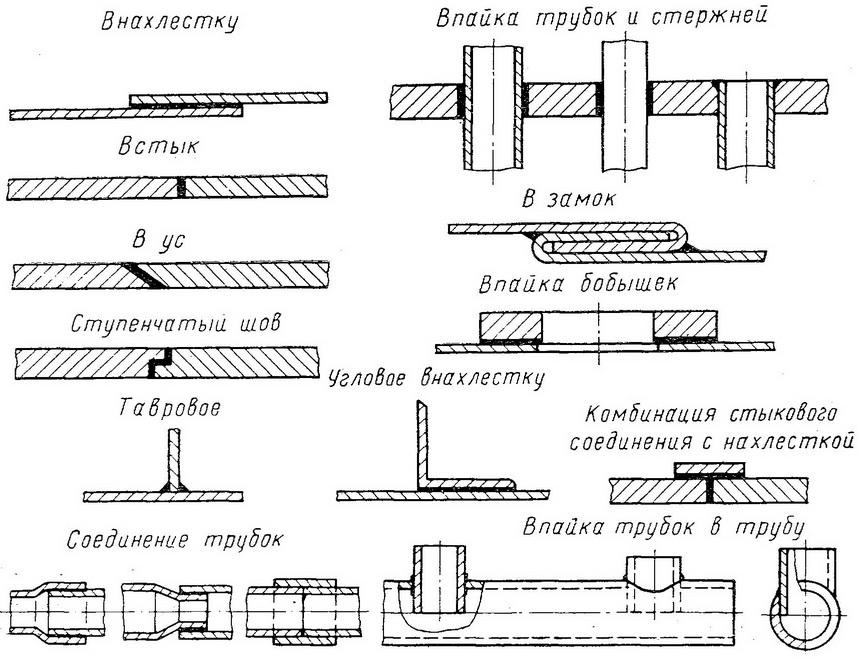
Заклепочные соединения
Заклепочные соединения используются для соединения листовых материалов.

Соединения деталей машин
Соединения в машинах и механизмах должны обеспечивать прочность, надежность и долговечность всей конструкции. При выборе типа соединения учитываются:
- Нагрузки (статические, динамические).
- Необходимость разборки.
- Точность соединения.
- Условия эксплуатации (температура, влажность).
- Материал деталей.
Пример: В редукторах часто используются шпоночные соединения для передачи крутящего момента, болтовые соединения для крепления корпусов, а также сварные соединения для прочных конструкций. Резьбовые соединения применяются для регулировки и фиксации элементов. В самолётостроении используются комбинации клеёных, заклёпочных и сварных соединений, в зависимости от нагрузок и конструкции.
Заключение
Соединения деталей являются важной частью любого механического устройства. Правильный выбор типа соединения, учет всех действующих нагрузок и условий эксплуатации обеспечивают надежную и долговечную работу механизмов. Понимание принципов расчета и конструирования соединений является ключевым для инженеров и конструкторов.
Проектирование, Напряжения, Применения
Введение
В предыдущей статье мы рассмотрели основные виды соединений деталей и их базовые расчеты. В этой статье мы углубимся в более сложные аспекты, такие как проектирование, анализ напряжений, специфические применения и современные тенденции в области соединений.
Проектирование соединений деталей
Проектирование соединений деталей — это комплексный процесс, требующий учета множества факторов. Основные этапы проектирования:
- Определение нагрузок:
Первым шагом является точное определение нагрузок, действующих на соединение. Это могут быть статические (постоянные), динамические (переменные), ударные нагрузки, а также вибрации. Необходимо учитывать не только величину нагрузок, но и их направление, а также распределение.
- Выбор типа соединения:
Исходя из характера нагрузок и условий эксплуатации выбирается оптимальный тип соединения (разъемное или неразъемное, механическое или сварное и т.д.). Этот выбор влияет на сложность сборки, возможность обслуживания и общую стоимость конструкции.
- Выбор материалов:
Материал соединительных элементов должен соответствовать материалу соединяемых деталей и обеспечивать необходимую прочность и долговечность соединения. Важно учитывать коррозионную стойкость, температурные условия и усталостную прочность.
- Расчет параметров соединения:
На этом этапе определяются геометрические параметры соединения: диаметры болтов, длина сварных швов, размеры шпонок, шлицев и т.д. Расчет проводится с учетом запаса прочности и требований к точности соединения.
- Анализ напряжений:
После расчета параметров выполняется анализ напряжений в соединении с использованием методов конечных элементов (МКЭ). Это позволяет определить критические области и обеспечить надежность конструкции.
- Проверка и тестирование:
После изготовления прототипа соединения проводятся испытания на прочность, герметичность и другие характеристики. Результаты тестирования используются для корректировки проекта.
Анализ напряжений в соединениях
Анализ напряжений является важным этапом проектирования, позволяющим выявить слабые места и оптимизировать конструкцию. Основные методы анализа:
- Аналитические методы:
Используют формулы и упрощенные модели для оценки напряжений. Подходят для простых соединений, но могут быть неточными для сложных геометрий и нагрузок.
- Метод конечных элементов (МКЭ):
МКЭ является мощным инструментом для анализа напряжений в сложных соединениях. Он позволяет точно моделировать геометрию и нагрузки и получать детальную картину распределения напряжений и деформаций.
- Экспериментальные методы:
Используются для проверки результатов аналитических и численных расчетов. Эксперименты могут включать измерение деформаций, напряжений с помощью тензодатчиков, а также разрушающие испытания.
Пример анализа напряжений в болтовом соединении
Предположим, нам нужно проанализировать напряжение в болтовом соединении, где болт М12 крепит две стальные пластины. Болт затянут с усилием 15 кН. Материал болта - сталь 8.8. Мы можем использовать МКЭ для моделирования и анализа.
Моделирование в МКЭ:
- Создается 3D-модель болта и пластин.
- Применяются граничные условия: закрепление пластин и усилие затяжки на болте.
- Проводится расчет распределения напряжений.
- Полученные результаты позволяют оценить напряжение в резьбе болта, в местах контакта и определить запас прочности.
Специфические применения соединений
Различные отрасли промышленности предъявляют особые требования к соединениям деталей. Рассмотрим несколько примеров:
Авиационная промышленность
В авиации соединения должны быть легкими, прочными и надежными. Часто применяются клееные соединения в сочетании с заклепочными. Для некоторых критических элементов используются сварные соединения из титановых сплавов. Важным фактором является усталостная прочность и устойчивость к вибрациям.

Автомобильная промышленность
В автомобилестроении широко применяются резьбовые соединения, сварка, точечная сварка, а также клееные соединения. Требования к соединениям — высокая производительность, низкая стоимость и надежность в условиях постоянных вибраций и нагрузок.
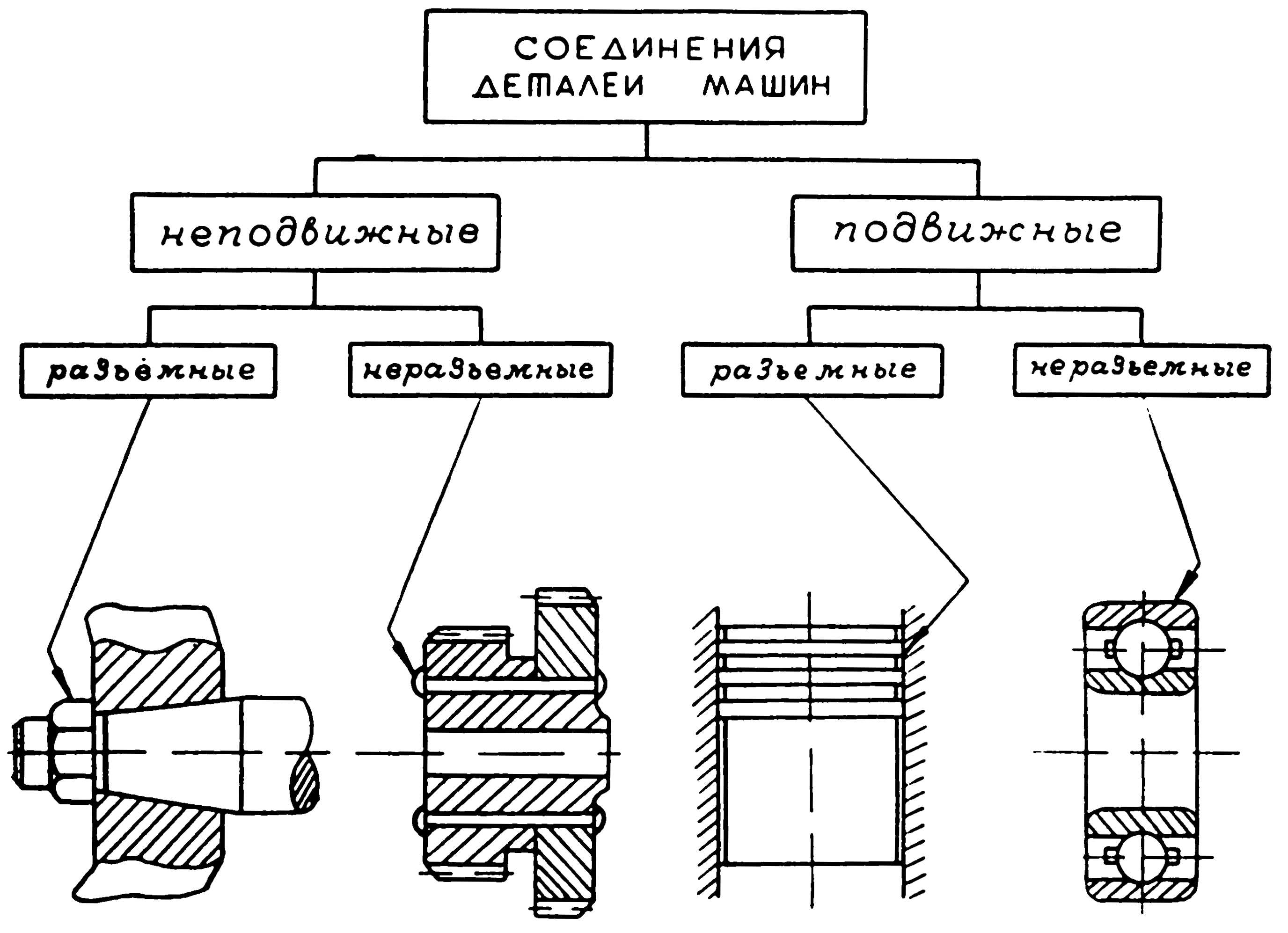
Электроника
В электронике используются миниатюрные соединения, такие как пайка, сварка, клеевые соединения для фиксации компонентов на печатных платах. Основные требования — точность, надежность и минимальный размер.
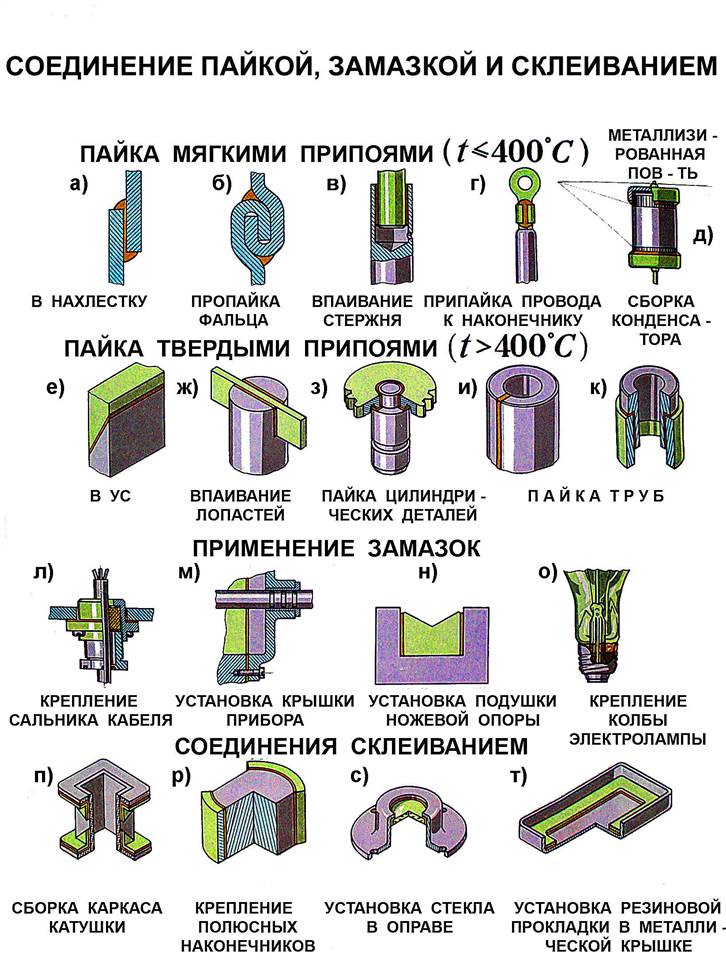
Строительство
В строительстве применяются болтовые и сварные соединения, а также специальные анкерные соединения для крепления конструкций. Требования включают высокую прочность, устойчивость к коррозии и воздействию окружающей среды.
Современные тенденции в области соединений
Современные технологии и материалы приводят к постоянному развитию в области соединений деталей. Основные тенденции:
- Использование композитных материалов:
Композитные материалы обладают высокой прочностью и низкой массой, что делает их привлекательными для авиации и автомобилестроения. Однако соединения композитов с металлами и другими материалами требуют специальных решений, таких как клееные соединения или специальные крепежные элементы.
- Аддитивные технологии:
3D-печать позволяет создавать сложные формы и интегрировать соединительные элементы непосредственно в детали. Это уменьшает количество необходимых элементов и повышает прочность соединений.
- Интеллектуальные соединения:
Разработка датчиков и систем мониторинга для контроля состояния соединений в режиме реального времени. Это позволяет обнаруживать дефекты на ранних стадиях и предотвращать аварии.
- Автоматизация процессов соединения:
Автоматизация сварки, сборки и других процессов соединения позволяет повысить точность, производительность и снизить стоимость.
- Разработка новых клеев:
Ведутся исследования по созданию клеев с повышенной прочностью, термостойкостью и устойчивостью к агрессивным средам.
Заключение
Проектирование и анализ соединений деталей – это сложный и многогранный процесс, который требует глубоких знаний и понимания механики материалов, технологий производства и современных тенденций. Правильный выбор типа соединения и его параметров обеспечивает надежность и долговечность конструкции. Новые материалы и технологии, такие как композиты, аддитивное производство и интеллектуальные системы мониторинга, открывают новые возможности в области соединений деталей.