Соединения деталей машин
Соединения деталей машин: Виды, Расчеты и Применения
Введение
Соединения деталей машин являются ключевым элементом любой механической конструкции. Они обеспечивают соединение отдельных компонентов в единую систему, позволяя передавать механические усилия и выполнять необходимые функции. В этой статье мы подробно рассмотрим различные виды соединений, их особенности, расчеты и области применения.
Классификация соединений деталей машин
Соединения деталей машин можно классифицировать по нескольким основным признакам:
- По возможности разборки:
- Неразъемные: Соединения, которые не могут быть разобраны без повреждения соединяемых элементов.
- Разъемные: Соединения, которые можно многократно собирать и разбирать без повреждений.
- По способу соединения:
- Механические: Соединения с использованием механических элементов (болты, винты, штифты).
- Сварные: Соединения, образуемые путем сварки.
- Клееные: Соединения, основанные на использовании клея.
- Пайка: Соединения, создаваемые с помощью припоя.
- По типу соединения:
- Жесткие: Соединения, которые обеспечивают неподвижность соединенных элементов друг относительно друга.
- Подвижные: Соединения, которые позволяют соединенным элементам перемещаться друг относительно друга.
- По назначению:
- Силовые: Соединения, предназначенные для передачи механической энергии.
- Конструкционные: Соединения, обеспечивающие сборку узлов.
- Герметичные: Соединения, предотвращающие утечку жидкости или газа.
Неразъемные соединения деталей машин
Неразъемные соединения обеспечивают прочное и долговечное соединение, но не предназначены для разборки без повреждения.
Сварные соединения
Сварка – это процесс соединения металлических деталей путем их нагрева до температуры плавления. Сварные соединения широко используются в машиностроении для создания прочных конструкций.
Пример: Сварка стальной рамы станка.
Типы сварки: Дуговая сварка, газовая сварка, контактная сварка.
Преимущества: Высокая прочность, герметичность, возможность соединения разнородных материалов.
Недостатки: Сложность демонтажа, нагрев и деформация соединяемых деталей.
Заклепочные соединения
Заклепки используются для соединения листов и других металлических деталей. Заклепка вставляется в отверстие, а затем деформируется для создания прочного соединения.
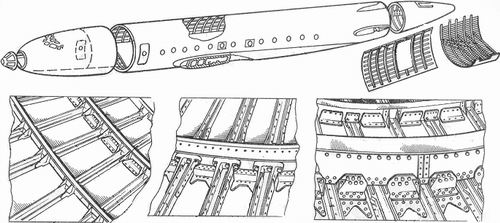
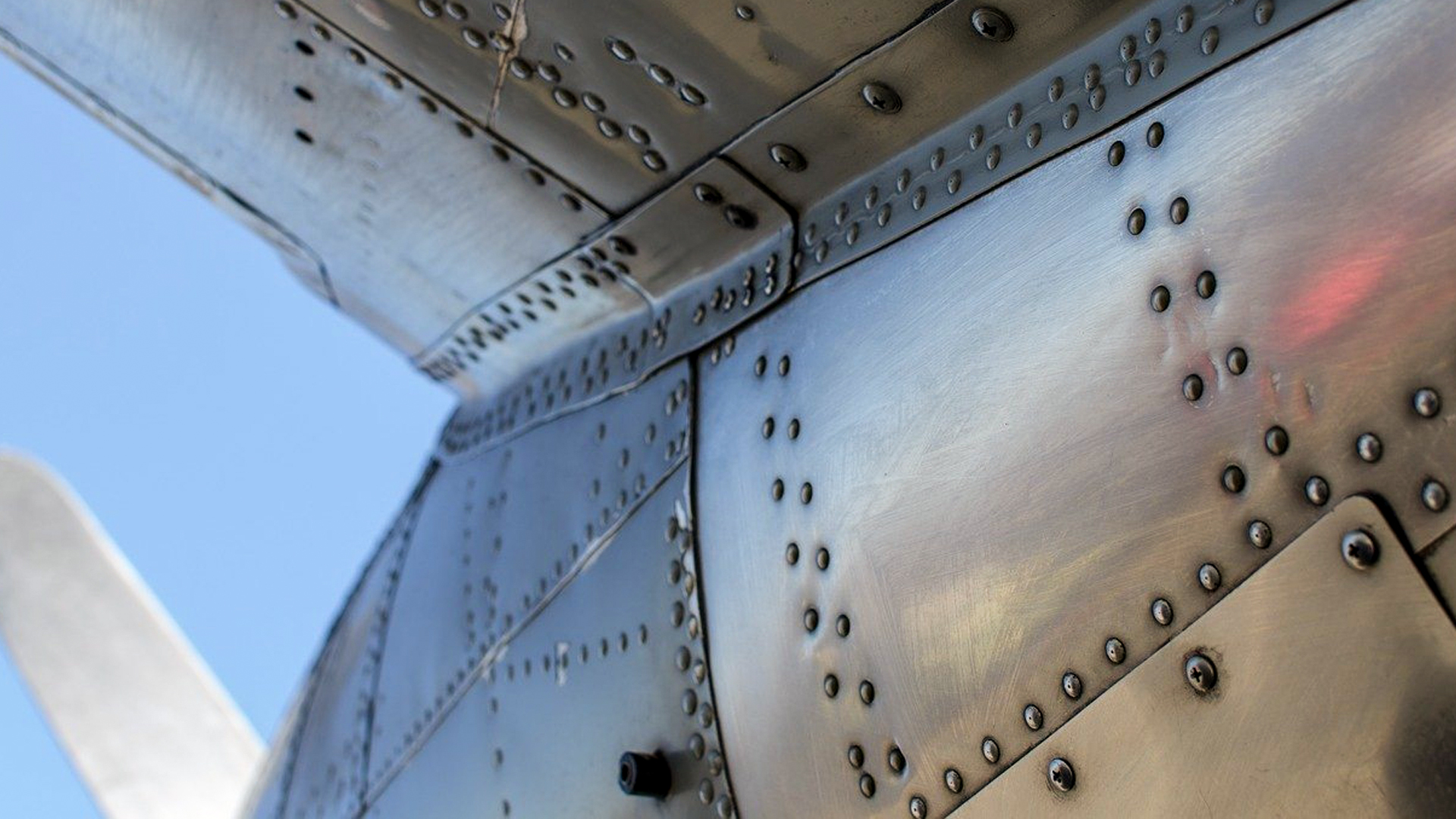
Пример: Соединение элементов обшивки самолета.
Преимущества: Простота, надежность, устойчивость к вибрациям.
Недостатки: Трудоемкость, необходимость специального оборудования.
Клееные соединения
Клеи используются для соединения металлических, пластиковых и композитных деталей. Клееные соединения обеспечивают равномерное распределение напряжения и высокую герметичность.
Пример: Соединение панелей кузова автомобиля.
Преимущества: Легкость, герметичность, возможность соединения разнородных материалов.
Недостатки: Чувствительность к температуре, ограниченная прочность.
Пайка
Пайка — процесс соединения металлических деталей с использованием расплавленного припоя. Припой расплавляется и заполняет зазор между деталями, образуя прочное соединение.
Пример: Соединение электрических контактов.
Преимущества: Электропроводность, герметичность, относительно низкая температура процесса.
Недостатки: Ограниченная прочность, необходимость контроля температуры.
Разъемные соединения деталей машин
Разъемные соединения позволяют многократно собирать и разбирать узлы без их повреждения.
Резьбовые соединения
Резьбовые соединения используют болты, винты, шпильки и гайки для соединения деталей. Это наиболее распространенный вид разъемных соединений в машиностроении.

Пример: Крепление крышки редуктора к корпусу.
Преимущества: Простота, универсальность, возможность регулировки.
Недостатки: Самоотвинчивание, концентрация напряжений в резьбе.
Шпоночные соединения
Шпонки используются для передачи крутящего момента между валом и вращающейся деталью. Шпонка вставляется в паз вала и детали, образуя механическую связь.

Пример: Крепление шкива на валу.
Преимущества: Простота конструкции, надежность передачи момента.
Недостатки: Концентрация напряжений в пазах вала и детали.
Шлицевые соединения
Шлицевые соединения используются для передачи больших крутящих моментов и точной фиксации деталей. Они представляют собой вал с продольными выступами (шлицами) и соответствующую деталь с внутренними пазами.
Пример: Промежуточный вал коробки передач с подшипниками, шестернями и деталями крепления:
1 — болт; 2— пружинная шайба; 3— крышка переднего подшипника промежуточного вала; 4—уплотнительная прокладка; 5—регулировочная шайба; 6—стопорное кольцо; 7—наружная обойма переднего подшипника; 8 —передний конический роликовый подшипник; 9 — упорная шайба: 10—шестерня постоянного зацепления; 11 — шестерня шестой передачи; 12 — наружная обойма заднего подшипника; 13 — задний конический роликовый подшипник; 14 — промежуточный вал; 15 — блок шестерен третьей и четвертой передач.
Преимущества: Высокая прочность, надежность, точная фиксация.
Недостатки: Сложность изготовления, высокая стоимость.
Штифтовые соединения
Штифты используются для точной фиксации положения двух или более деталей. Штифты могут быть цилиндрическими, коническими или пружинными.
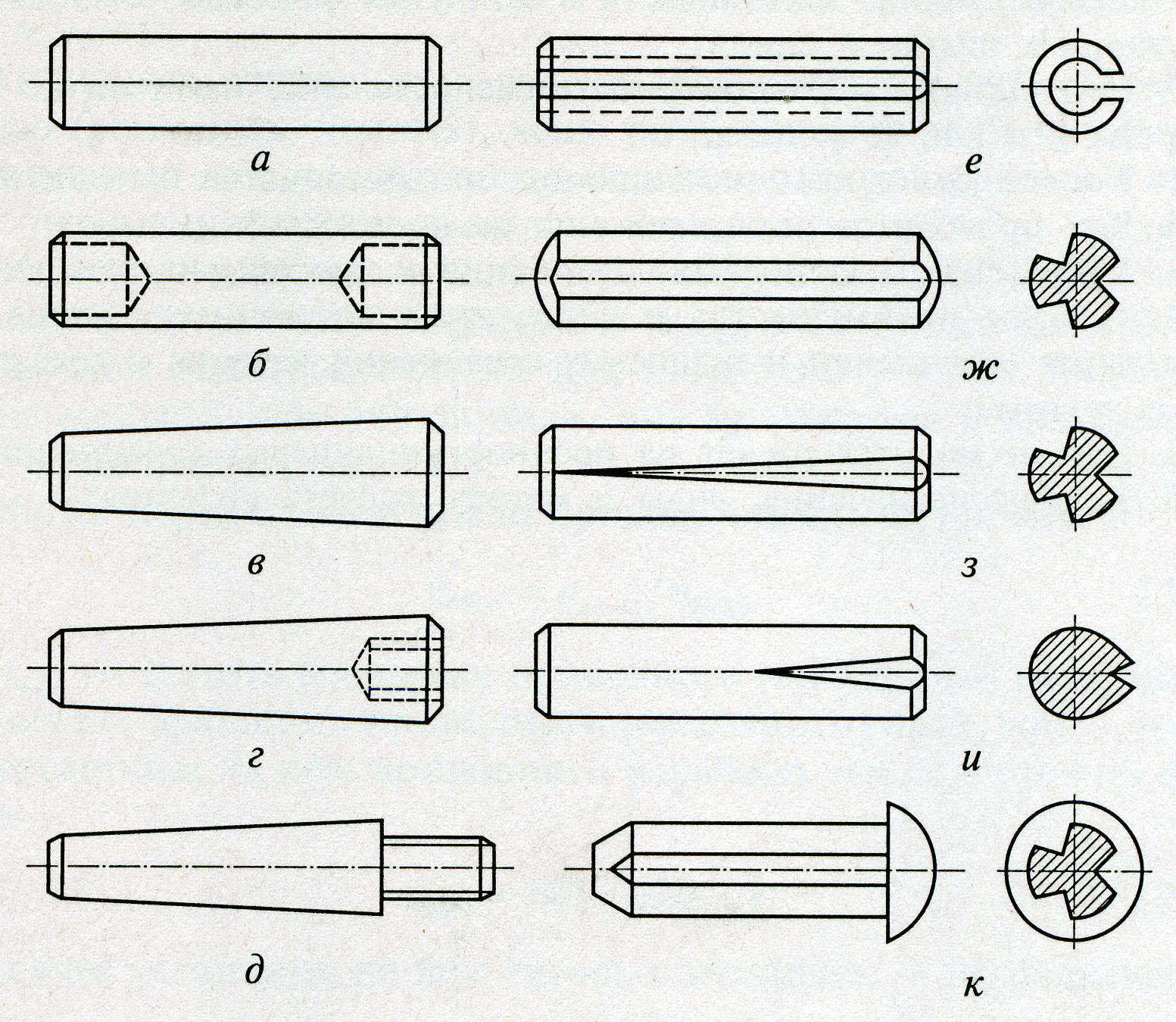
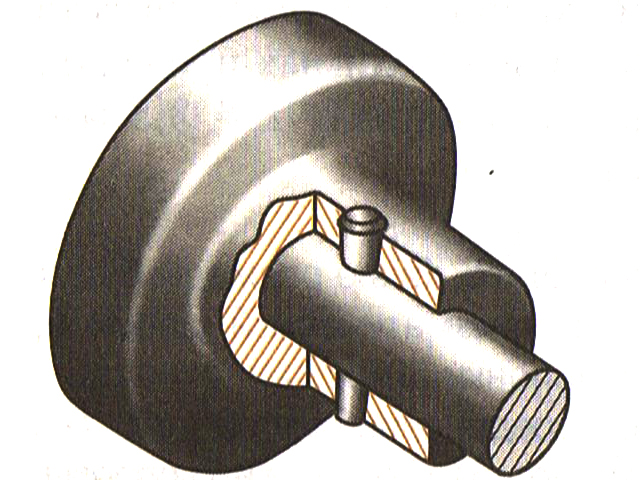
Пример: Основные типы штифтов:а – цилиндрический; б – цилиндрический с отверстиями для расклепывания;
в – конический; г – конический с внутренней резьбой; д – конический с наружной резьбой; е – пружинный; ж – к – просеченные (с канавками)
Преимущества: Простота, надежность, точная фиксация.
Недостатки: Не предназначены для передачи больших нагрузок.
Клиновые соединения
Клиновые соединения используются для фиксации деталей и передачи крутящего момента. Клин вставляется в пазы вала и детали, создавая плотную посадку.
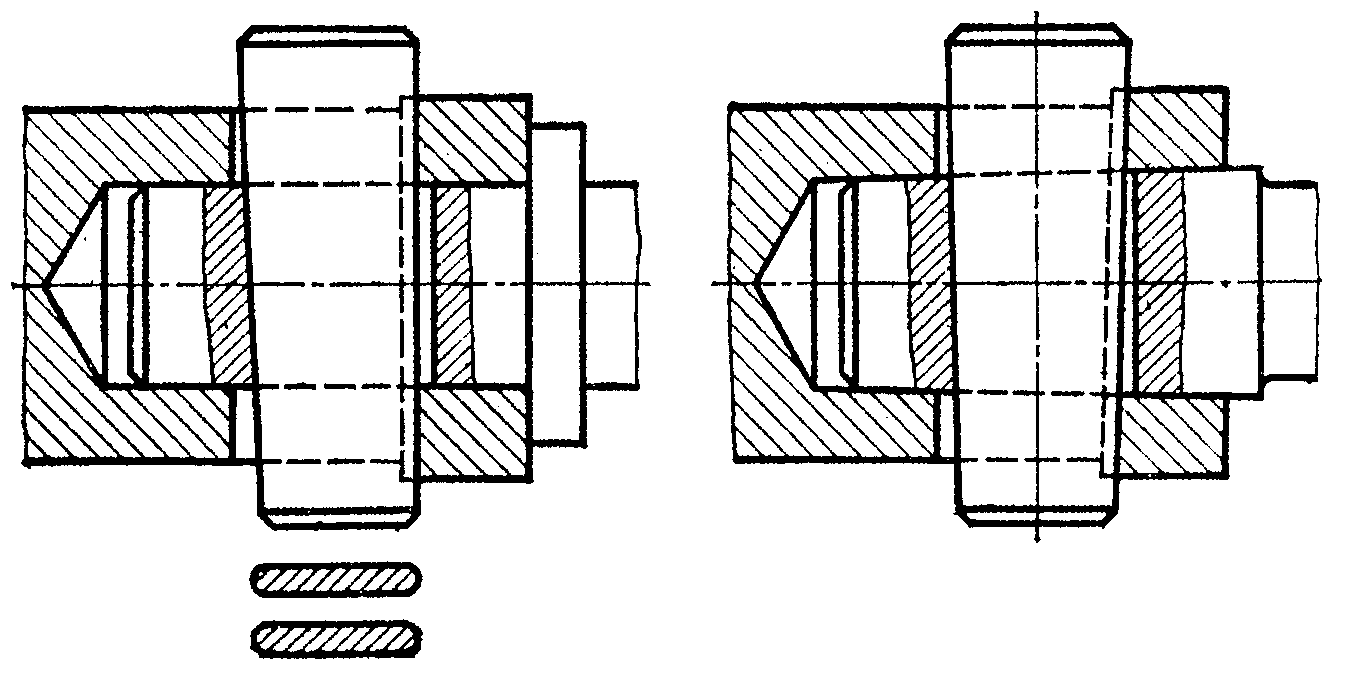
Пример: Клиновые соединения стержня со втулкой: сопряжение по цилиндрической поверхности и по торцу (а), по конической поверхности (б)
Преимущества: Простота, надежность, возможность регулировки.
Недостатки: Необходимость точной подгонки клина.
Подвижные соединения деталей машин
Подвижные соединения позволяют элементам перемещаться относительно друг друга. Основные типы:
- Шарнирные соединения: Позволяют вращательное движение вокруг оси (например, шарниры в подвеске автомобиля).
- Скользящие соединения: Позволяют линейное перемещение (например, поршень в цилиндре).
- Подшипники качения и скольжения: Обеспечивают вращательное движение с минимальным трением.
- Направляющие: Обеспечивают точное линейное или криволинейное перемещение.
Расчет соединений деталей машин
Расчет соединений деталей машин необходим для определения их прочности, надежности и долговечности. Примеры расчетов:
Расчет резьбового соединения
Задача: Определить усилие затяжки болта.
Формула: Fзатяжки = σдоп * Aрезьбы, где σдоп - допустимое напряжение, Aрезьбы - площадь сечения резьбы.
Пример: Болт М10 (диаметр резьбы 10 мм), сталь 8.8 (σдоп ≈ 420 МПа), Aрезьбы ≈ 55 мм2. Fзатяжки= 420 * 55 = 23100 Н = 23.1 кН
Расчет шпоночного соединения
Задача: Проверить прочность шпонки на смятие.
Формула: σсм = F / Aсм, где σсм - напряжение смятия, F - сила, действующая на шпонку, Aсм - площадь смятия.
Пример: Момент на валу M = 200 Нм, диаметр вала d=30 мм, шпонка 8х7 мм, длина 50 мм. F = M/(d/2) = 200/(0.03/2) = 13333 Н. Aсм= (7мм/2)*50мм =175 мм2, σсм = 13333/175=76.2 МПа.
Расчет сварного соединения
Задача: Определить толщину сварного шва.
Формула: t = Aшва / l, где t - толщина шва, Aшва - площадь шва, l - длина шва.
Пример: Усилие F=10000 Н, σдоп=200 МПа, длина шва l=100 мм. Aшва=F/σдоп =10000/200=50 мм2. Тогда толщина шва t=50/100=0.5 мм. В реальности, толщина шва должна быть не менее толщины самого материала, т.е. 10 мм.
Примеры соединений деталей машин
Редукторы: Используют резьбовые соединения для крепления корпусов, шпоночные и шлицевые соединения для передачи крутящего момента. Подшипники обеспечивают вращение валов.
Станки: Применяют сварные и болтовые соединения для создания прочных станин, а также направляющие для точного перемещения инструментов.
Двигатели: Используют резьбовые соединения, шпоночные соединения и штифты для точной сборки механизмов.
Автомобили: Сочетают в себе резьбовые, сварные, заклепочные и клееные соединения для различных элементов кузова и подвески.
Заключение
Соединения деталей машин играют важнейшую роль в конструировании и эксплуатации механических систем. Понимание различных видов соединений, их преимуществ и недостатков, а также умение проводить расчеты, позволяют создавать надежные и эффективные механизмы. Правильный выбор и проектирование соединений гарантируют долговечность и безопасность работы машин и оборудования.
Анализ напряжений в соединениях
Анализ напряжений является ключевым этапом при проектировании соединений, обеспечивающим их прочность и надежность. Существуют аналитические и численные методы анализа.
Аналитические методы
Аналитические методы используют формулы и упрощенные модели для расчета напряжений. Они применяются для простых соединений, но могут быть неточными для сложных геометрий.
Пример: Расчет напряжений в болтовом соединении при растяжении.
Рассмотрим соединение двух пластин болтом M12, при растягивающей нагрузке F=30 кН. Материал болта сталь 8.8. Площадь сечения резьбы Aрезьбы= 84.3 мм2.
Напряжение в болте σ = F / Aрезьбы = 30000 Н / 84.3 мм2 = 356 МПа.
Допустимое напряжение для стали 8.8 около 640 МПа/1.5=426МПа > 356 МПа, следовательно прочность обеспечена
Численные методы (МКЭ)
Метод конечных элементов (МКЭ) позволяет моделировать сложные геометрии и нагрузки, предоставляя точную картину распределения напряжений. Это критически важно для сложных соединений.
Пример: МКЭ анализ сварного соединения.
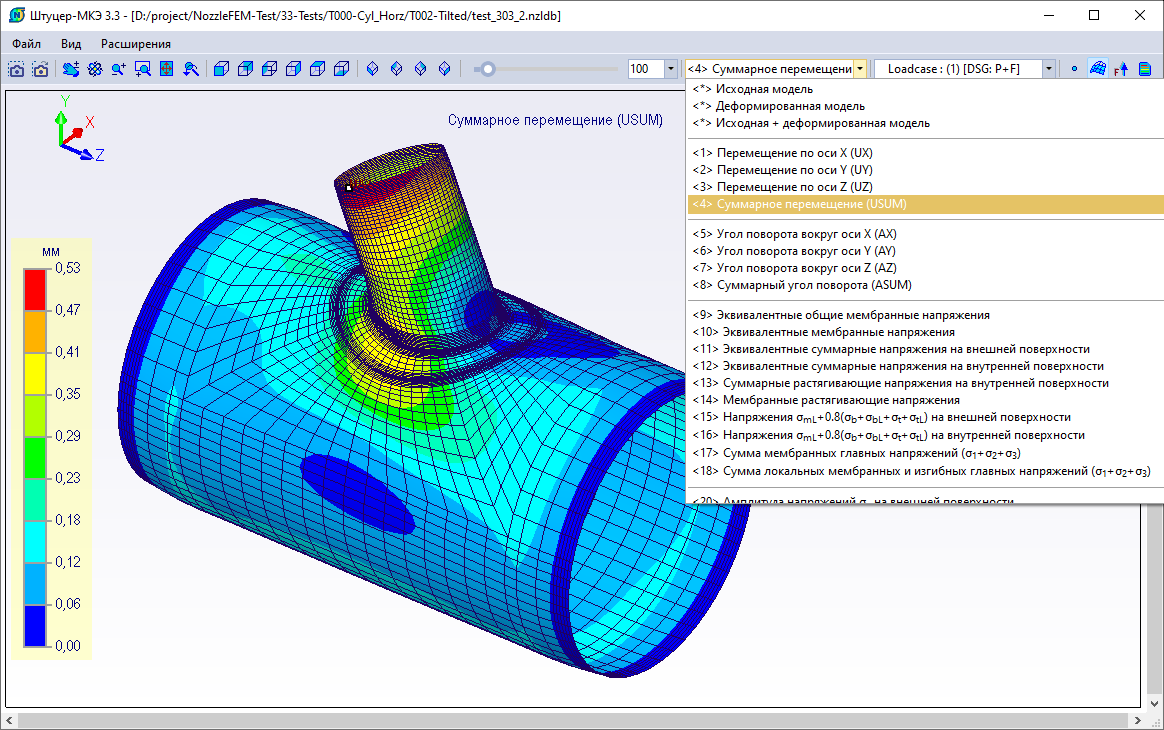

При моделировании сварного соединения, используются элементы конечных размеров, на которые разбивается вся конструкция. Задаются характеристики материала, нагрузки и граничные условия. Далее выполняется расчёт и строятся диаграммы напряжения в сварном шве. Результаты позволяют оценить прочность сварного соединения.
Программное обеспечение: ANSYS, SolidWorks Simulation, Abaqus.
Факторы, влияющие на прочность соединений
Прочность соединений зависит от множества факторов, которые следует учитывать при проектировании.
- Материал деталей:
Прочность и характеристики материалов напрямую влияют на прочность соединения. Важно учитывать предел текучести, предел прочности, усталостную прочность.
- Геометрия соединения:
Форма и размеры соединительных элементов влияют на распределение напряжений. Концентраторы напряжений (острые углы, вырезы) следует минимизировать.
- Точность изготовления:
Допуски и посадки влияют на плотность соединения и распределение нагрузки. Неточности могут приводить к перегрузкам и преждевременному разрушению.
- Условия эксплуатации:
Температура, влажность, коррозионная среда, вибрации и ударные нагрузки могут снижать прочность соединения. Необходимо учитывать все возможные воздействия.
- Качество сварки, клея, пайки:
Некачественная сварка или неверный подбор клея могут ослабить соединение. Важен контроль качества процессов.
- Усилие затяжки резьбовых соединений:
Правильная затяжка болтов и винтов обеспечивает надежное соединение, избыточная затяжка может привести к повреждению резьбы.
- Износ и усталость:
Соединения подвержены износу и усталостному разрушению при переменных нагрузках. Необходим расчет на усталость при проектировании.
Специфические применения соединений в машиностроении
Различные отрасли машиностроения предъявляют особые требования к соединениям. Рассмотрим несколько примеров.
Аэрокосмическая промышленность
В авиации и космонавтике соединения должны быть легкими, прочными и надежными. Применяются:
- Клееные соединения: Для обшивки фюзеляжей, крыльев.
- Заклепочные соединения: Для крепления элементов конструкции.
- Резьбовые соединения из титановых сплавов: Для критически важных элементов.
- Сварка трением и лазерная сварка: Для соединения высокопрочных материалов.
Судостроение
В судостроении соединения должны быть устойчивыми к коррозии, воздействию воды и больших нагрузок. Применяются:
- Сварные соединения: Для корпуса судна и других крупных элементов.
- Болтовые соединения: Для крепления оборудования и механизмов.
- Клепаные соединения: В исторических конструкциях.
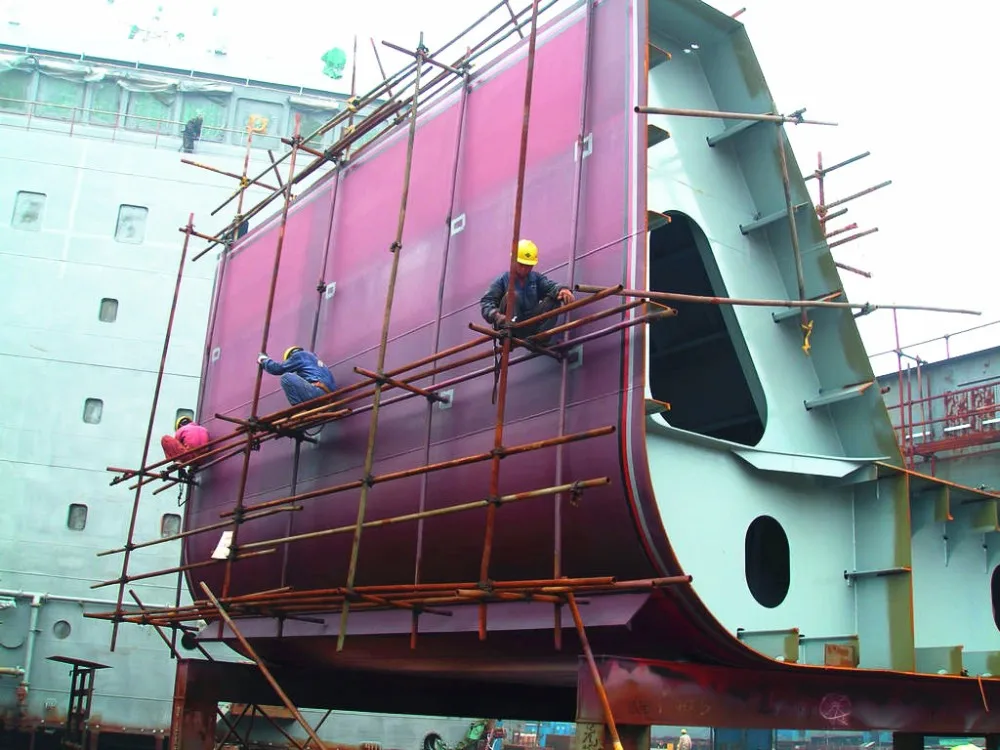
Тяжелое машиностроение
В тяжелом машиностроении соединения должны выдерживать большие нагрузки и обеспечивать долговечность. Применяются:
- Сварные соединения: Для рам, опорных конструкций, мостов.
- Шлицевые соединения: Для передачи больших моментов.
- Резьбовые соединения: Для крепления тяжелых узлов.

Станкостроение
В станкостроении соединения должны обеспечивать высокую точность и жесткость. Применяются:
- Шпоночные и шлицевые соединения: Для передачи вращательного движения.
- Резьбовые соединения: Для точной регулировки положения элементов.
- Сварные конструкции: Для обеспечения жесткости.
Современные технологии в области соединений
Современные технологии постоянно развивают методы соединения деталей, улучшая их прочность, надежность и эффективность.
Лазерная сварка
Лазерная сварка позволяет создавать точные и прочные швы с минимальной зоной термического воздействия, что особенно важно для чувствительных материалов.
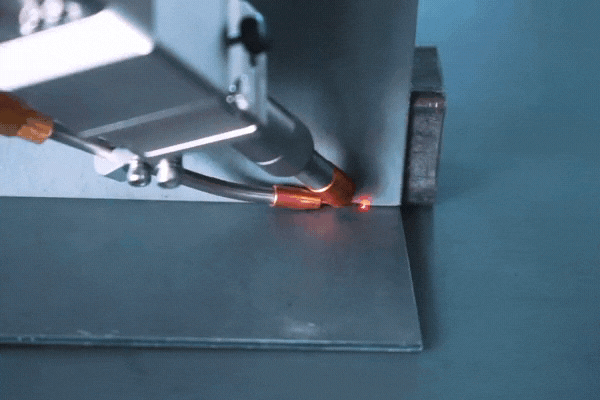
Сварка трениемс перемешиванием
Сварка трением с перемешиванием (Friction Stir Welding) обеспечивает высококачественные соединения без расплавления материала, что позволяет избежать деформаций и улучшить прочность шва.
Аддитивные технологии (3D-печать)
3D-печать позволяет создавать сложные детали с интегрированными соединительными элементами, уменьшая количество деталей и повышая прочность конструкции. Эта технология находит широкое применение в прототипировании и мелкосерийном производстве.

Интеллектуальные соединения
Разработка датчиков и систем мониторинга для контроля состояния соединений в режиме реального времени позволяет обнаруживать дефекты на ранних стадиях и предотвращать аварии. Эти технологии применяются в аэрокосмической, транспортной и энергетической отраслях.
Новые клеи и композитные материалы
Исследования в области полимерной химии и материаловедения привели к созданию новых клеев с повышенной прочностью и термостойкостью, а также композитных материалов с улучшенными характеристиками. Это позволяет создавать более легкие и прочные конструкции.
Заключение
Соединения деталей машин являются неотъемлемой частью любого механического устройства. Правильный выбор типа соединения, его параметров и учет всех факторов, влияющих на его прочность и долговечность, являются ключом к созданию надежных и эффективных механизмов. Современные технологии и разработки постоянно совершенствуют методы соединения, открывая новые возможности для инженеров и конструкторов.